Key Takeaways:
- The reverse optical engineering process includes understanding the lens’s use, disassembly, data recording, and deriving new designs.
- Reverse optical engineering involves analyzing and recreating existing optical components when original designs are unavailable.
- The goal is to produce high-quality lenses that meet customer needs through rigorous testing.
What is Reverse Optical Engineering?
Optical reverse engineering involves understanding the functionality of existing optical components or systems through thorough analysis. This process enables the recreation or enhancement of these components. It’s useful when you don’t have the original design or want to make a better version of something that already exists. This can be used to create a custom optic system for specific needs, to identify the original engineering work, or to copy complex designs in a faster and cheaper way. Furthermore, this process empowers individuals to refine a system’s focal point and capture intricate object details, facilitating further analysis and manufacturing based on the refined design.
The difference between normal design lens workflow and optical reverse engineering
The traditional design workflow is “from scratch”, that is, creating a product from scratch, as shown in Figure 1, and machining the parts before assembling the lens. But there is also design work that needs to be reverse-engineered for a variety of reasons. For example, the original manufacturer of a certain lens has stopped production, but there is still a small amount of demand in the market, and customers need to manufacture products with similar performance to meet the use, then reverse engineering is needed.
“Reverse engineering” refers to the reproduction process of a product design technology. Starting with an existing product, reverse the process and disassemble each part or layer, as shown in Figure 2, and disassemble the lens to test the part parameters. The goal is to make products that function similarly, but not exactly the same.
Optical reverse engineering offers a cost-effective way to create high-quality computer aided design (CAD) models of existing optical components, enabling replication or the development of improved designs.
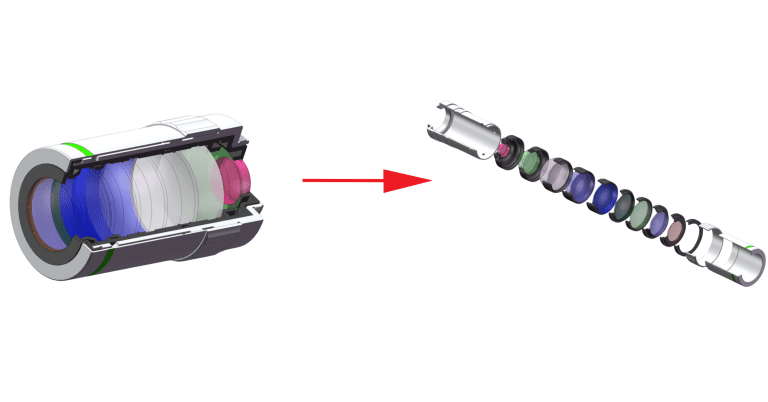
Reverse Optical Engineering Process
The reverse process of optical lenses generally consists of the following steps:
- Understand the background of the lens
The ultimate goal of lens reverse is to create lenses that can meet customer needs. Therefore, before the work is carried out, it is necessary to understand the use scenario and application purpose of the product in detail, and have a full understanding of the lens to form the concept of the lens light path.
- Lens data acquisition and processing
By means of measurement and testing, the performance parameters and data of the lens, including optical properties, mechanical properties, etc., are obtained, and these data are processed and analyzed.
The focal length, entry pupil, NA, field of view, band (test coating band after disassembly), and working distance of the lens are all important parameters, which need to be accurately tested before the next step. The performance characterization of the lens, such as MTF, wavefront difference or projection effect, provides the target for the effect to be achieved by reverse engineering.
- Disassemble the lens
Disassemble the existing lens to obtain its internal structure and components. Lens disassembly is a destructive test, therefore, it generally requires customers to provide more than 2 sets of products.
- Data acquisition of components
After the product is disassembled, it is crucial to record the parts contained in the lens in detail and the relationships between them before proceeding to the next step of analysis.
When assessing the structural elements within a lens, it’s typically essential to examine their mechanical dimensions. Similarly, for optical components, identifying the type of component precedes analysis. Take, for instance, a spherical lens; besides evaluating its basic mechanical size, it’s imperative to test its surface curvature, surface shape accuracy, and the reflectance of the film layer, among other factors. Additionally, determining the material of the lens often involves destructively testing the optical part to ascertain parameters such as the refractive index and Abbe number.
- Derivation design
After obtaining sufficient information about the component, the corresponding parameters can be imported into the optical design software to deduce whether the performance of the constructed lens is consistent with the application and lens performance.
Often, due to the existence of test bias, the directly generated design does not meet expectations, and still needs to be optimized, or even improved, to meet the needs of use. In this process, the new design often deviates from the original design. But no matter how the design changes, the ultimate goal is to satisfy the customer’s application.
- Manufacturing and testing
Manufacture and test according to the optimized design and verify the performance of the lens.
Conclusion
With the help of Avantier’s unique inspection methods and rigorous validation procedures, optical reverse engineering ensures the accuracy and quality of the generated design data.
Lens reverse engineering is a complex technology that requires certain knowledge and experience in the manufacturing process, including diamond turning and injection molding, optical, mechanical, and other fields, as well as special professional testing equipment. More importantly, it is necessary to abide by the relevant laws, regulations, and ethics and respect the intellectual property rights and patents of others. Please contact us if you’d like to request a quote on your next project.
GREAT ARTICLE!
Share this article to gain insights from your connections!