Key Takeaways:
- Avantier is dedicated to enhancing production feasibility through innovative methods and technologies, particularly in spherical and aspherical lens manufacturing.
- Utilizing techniques like numerical control cold processing, compression molding, and injection molding, Avantier ensures precision in both traditional spherical lenses and the more challenging aspherical surfaces.
- We employ advanced tools such as the SPS-200 instrument, guaranteeing consistent accuracy across spheres and aspheres.
- Avantier’s commitment to close collaboration with customers allows for customized solutions that meet specific production objectives.
Spherical lens and Aspheric Manufacturing
Avantier has always been committed to improving customer production feasibility. We focus on research and development and innovation, continuously introducing new technologies and solutions to meet customers’ ever-changing requirements. Furthermore, Avantier emphasizes close cooperation with customers, gaining insight into their needs, and providing customized solutions to help customers achieve production goals and enhance competitiveness.
Manufacture Methods
Aspherical surface processing method | Compared with traditional lens machining, the aspherical surface is much more difficult to process because of the different curvature of each point on the surface.
At present, the main processing methods are numerical control cold processing, compression molding, injection molding. |
Numerical control cold processing method | “Cold processing method” refers to the processing method that does not produce high temperature and high temperature reaction in the processing process, which belongs to removal processing.The traditional cold processing method includes blank shaping, rough grinding, fine grinding, polishing, and edging. |
The cold processing of aspherical lenses can be divided into two stages: milling forming and precision polishing. In the milling stage and polishing stage, diamond single point turning, CNC or mechanical arm small grinding head can be used. Diamond single point turning is good at processing infrared materials and metal materials, such as zinc sulfide, zinc selenide, germanium. CNC is good at processing symmetrical asperse. The advantage of the small grinding head is that the shape and size of the aspherical surface are not too restricted. The polished component has good roughness and better surface shape error. When the accuracy of the aspherical surface is high, it is necessary to further use magneto-rheological polishing technology (MRF) and ion beam polishing technology (IBF) to achieve surface shape refinement, both of which have high requirements for the pre-polished and semi-finished product surface shape. In the finishing stage, the traditional hand repair method can also be used, and the hand repair can save equipment costs, but the accuracy of the hand repair depends on the experience of the technician; plus, the requirements for personal ability are high.
The process cycle of cold processing is long, and the efficiency is low, which cannot meet the requirements of mass production. However, cold processing is suitable for small batch and high precision aspherical lens processing.
Compression molding
Compression molding is one of the alternatives to the traditional machining methods of aspherical lenses. Compression molding is a method of softening the optical glass by heating it to have enough plasticity, and then pressing it with an aspherical mold to obtain an aspherical lens. This processing method usually uses glass materials with a lower melting point.
The cost of forming aspherical lenses is low, but the manufacturing cost of aspherical molds is very high. Aspherical molds must use materials that can withstand high temperatures and keep the surface smooth. The mold is generally turned by a single point diamond lathe, and the product accuracy of the molding method will be limited by the surface accuracy of the mold. In the case of good mold surface shape, the molded lens can ensure high precision and meet the needs of conventional precision lenses. The process parameters of molding are more complex, and the temperature, pressure and other parameters need to be accurately controlled.
The conventional diameter of a compression molding glass aspherical lens is less than 50mm. The process of aspherical surface molding is stable, and the processing cycle is short, but due to the high mold manufacturing cost, it is generally used for mass production of aspherical lenses.
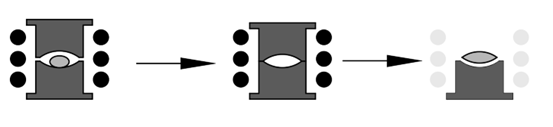
Injection molding
Injection molding is one of the processing methods of plastic aspherical lenses. Plastic aspherical lenses have the advantages of light weight, low cost, and the ability to be processed together with mounting parts. Common optical plastics are PMMA, PC, etc.
By using an injection molding machine, a certain amount of plastic is heated into a fluid, injected into the stainless-steel mold, formed after heating and pressurizing, and after a certain period of cooling, the parts are separated from the mold, and the aspherical lens can be obtained. Later, it can also be polished and strengthened according to specific needs to improve the finish, durability, and other properties of the components.
Compared with compression molding molds, injection molds have lower operating temperatures and lower processing requirements. Multiple chambers can usually be designed in a mold, so that multiple components can be obtained at a time. The thermal expansion coefficient of optical plastics is relatively large, and the difference between the expansion coefficient and the mold is large when cooling, so the surface accuracy of the aspherical lens manufactured by injection molding is usually low, which is suitable for the manufacture of plastic aspherical lenses with large batches, moderate quality, and low thermal stability requirements.
Our Instrument In Service
Avantier utilizes the SPS-200 instrument in our lens manufacturing process to ensure consistent polishing accuracy across a wide range of optical shapes. The SPS-200 offers polishing in both Synchrospeed and Variospeed modes, along with adaptive deterministic pre- and corrective polishing technology (ADAPT). This combination enables us to achieve highly accurate yet efficiently produced aspheres and freeforms.
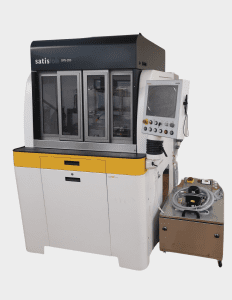
Specifications
Geometries | Spheres, Aspheres, Cylinders, Toroids, Freeforms, & Other Optical Surfaces |
Working range | Spherical Ø 10–200 mm (up to 300 mm with restrictions)Aspherical Ø 10–300 mm |
Dimensions (W x D x H) | 1200 x 1850 x 1970 mm47.2 x 72.8 x 77.5 inches |
Weight | Approximately 3200 kg / 7054 lb |
Flexibility:
- Our modular machine design is tailored to meet your specific needs, ensuring adaptability to diverse production requirements.
- Versatility is at the core of Satisloh SPS-200, as it is capable of processing spheres, aspheres, freeform surfaces, edges, chamfers, and various other processes. It also offers comprehensive solutions for optical component manufacturing.
- With an extended Y-axis and diverse spindle combinations, Satisloh SPM-200 offers maximum flexibility, accommodating a wide range of grinding and polishing tasks.
Reliability:
- Satisloh SPM-200 is built on a foundation of high stability, thanks to our unique and proven polymer concrete base and vibration damping machine feet, which ensure consistent performance even under demanding conditions.
- Precision is guaranteed with direct-driven and water-cooled spindles and axis, maintaining tight tolerances and superior surface finishes.
- Utilizing 3D process simulation enhances process safety, minimizing risks and optimizing production efficiency.
- Optional air bearing workpiece spindle ensures excellent surface finish during the grinding process, meeting the highest quality standards.
- Integrated quality control system effectively compensates for inaccuracies caused by tool wear, ensuring reliable and consistent results over time.
Efficiency:
- Leveraging unique dual tool spindle technology and additional horizontal spindle options, setup times are reduced, and multiple processes can be performed seamlessly without the need for retooling.
- Cost-effective production is achieved through grinding in disc and cup-wheel modes, optimizing resource utilization and maximizing output.
- Our polishers feature integrated dressing spindles, streamlining operations and enhancing efficiency throughout the polishing process.
In conclusion, Avantier delivers customized solutions that not only meet but surpass production objectives, enhancing competitiveness in the market by prioritizing close collaboration with customers and understanding their specific needs. Through the utilization of advanced methods such as numerical control cold processing, compression molding, and injection molding, Avantier ensures precision and efficiency in manufacturing a diverse range of optical components. Furthermore, by integrating cutting-edge technologies like the SPS-200 instrument, Avantier ensures consistent polishing accuracy across various optical shapes, reaffirming our dedication to excellence in every aspect of manufacturing processes. For more information on manufacturing limits or to make a custom metrology request for a quote on your next project, please contact us.