Reverse Optical Engineering is a complex and systematic process that involves the meticulous deconstruction and analysis of existing optical components, lenses, or assemblies to understand their design, specifications, and manufacturing techniques. By employing a combination of high precision metrology tools and engineering expertise, this approach enables the replication or modification of the original design, leading to the development of high-quality, custom optics or optical systems that are both cost-effective and reliable.
The first crucial step in reverse optical engineering is the disassembly of the finished product or optical component under investigation. This process requires utmost care to avoid any damage to the delicate parts. Specialized tools and techniques are employed to carefully dismantle the optical system, allowing for individual examination and measurement of each component.
The process of reverse optical engineering heavily relies on high precision metrology to ensure accurate and detailed measurements. Metrology tools play a vital role in capturing various parameters such as lens curvature, thickness, focal length, and surface quality. These measurements are critical for understanding the intricacies of the existing optical system and informing the design of the reverse-engineered product.
Several common types of testing equipment are involved in reverse engineering.
The Panasonic UA3P-300 3D Profilometer and Zygo 3D Optical Surface Profiler are utilized for 3D visualization and data grouping. These techniques may include 3D scanning, coordinate measuring machines (CMM), or optical measurement systems to capture geometry, dimensions, and surface details.
For surface measurement, Zygo Verifire Interferometer, Taylor Hobson Optical Profilometer, and Radius Test Benches are employed, depending on the surface shape and specific specifications that need to be measured.
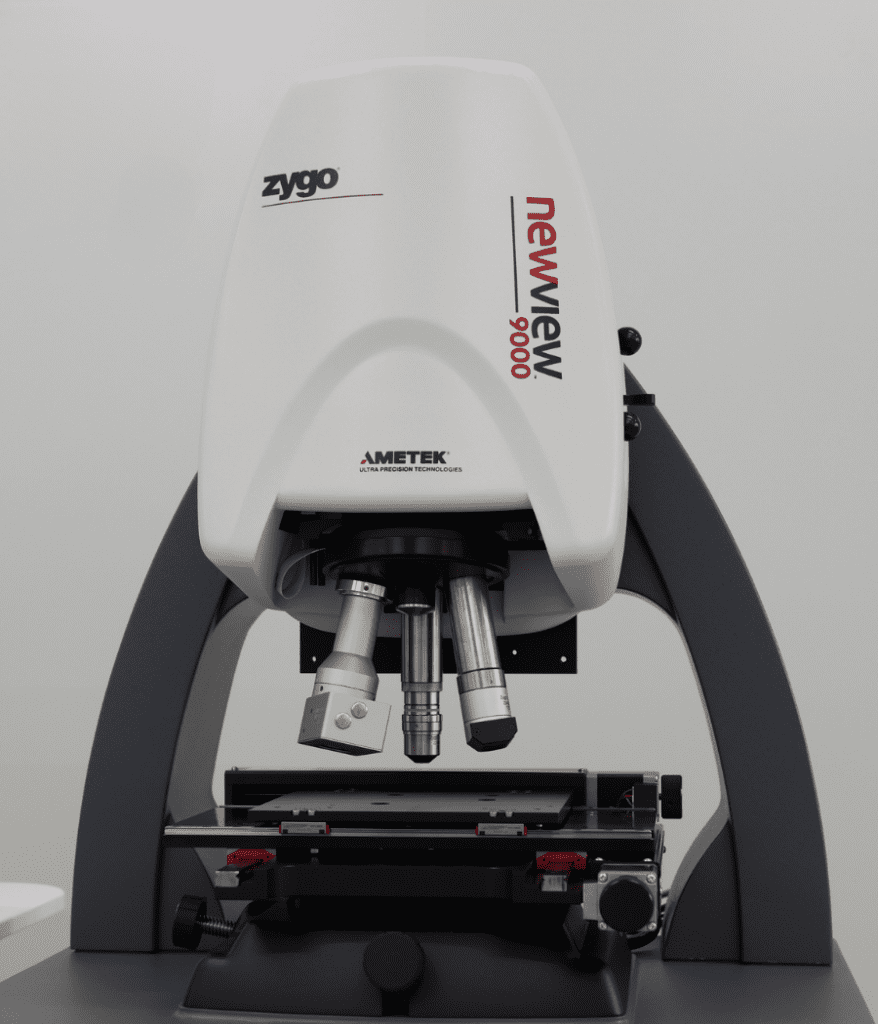
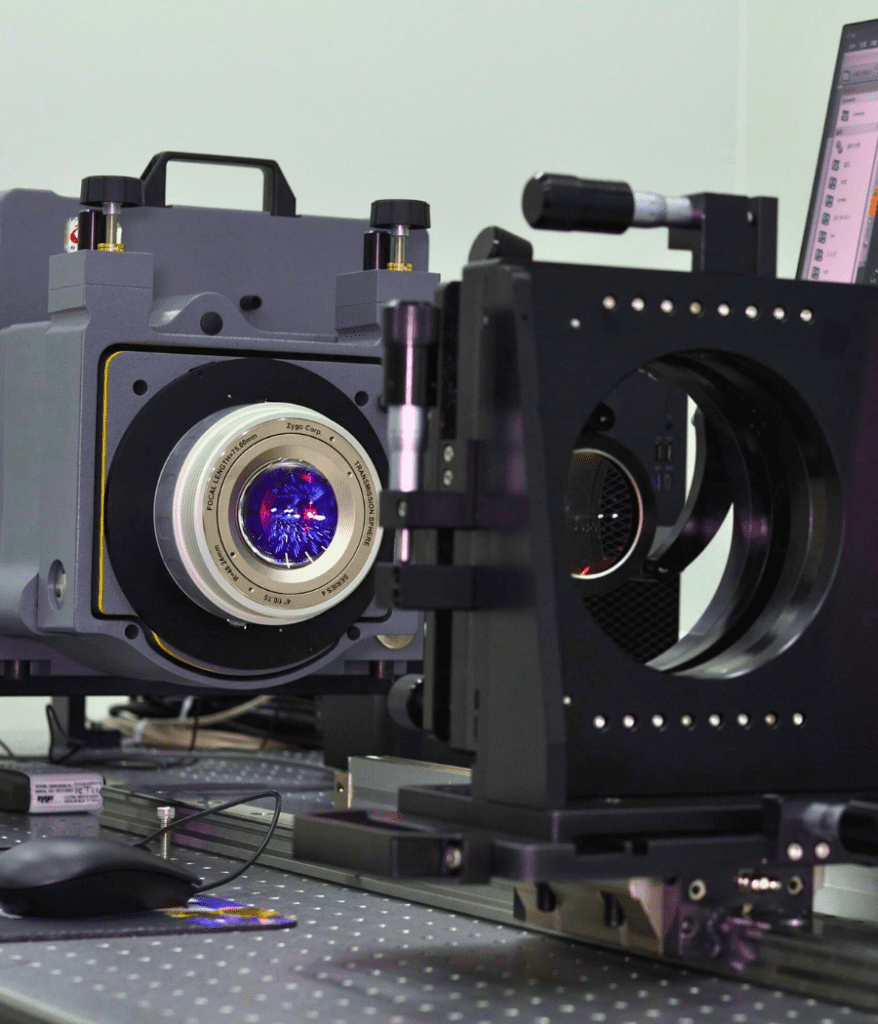
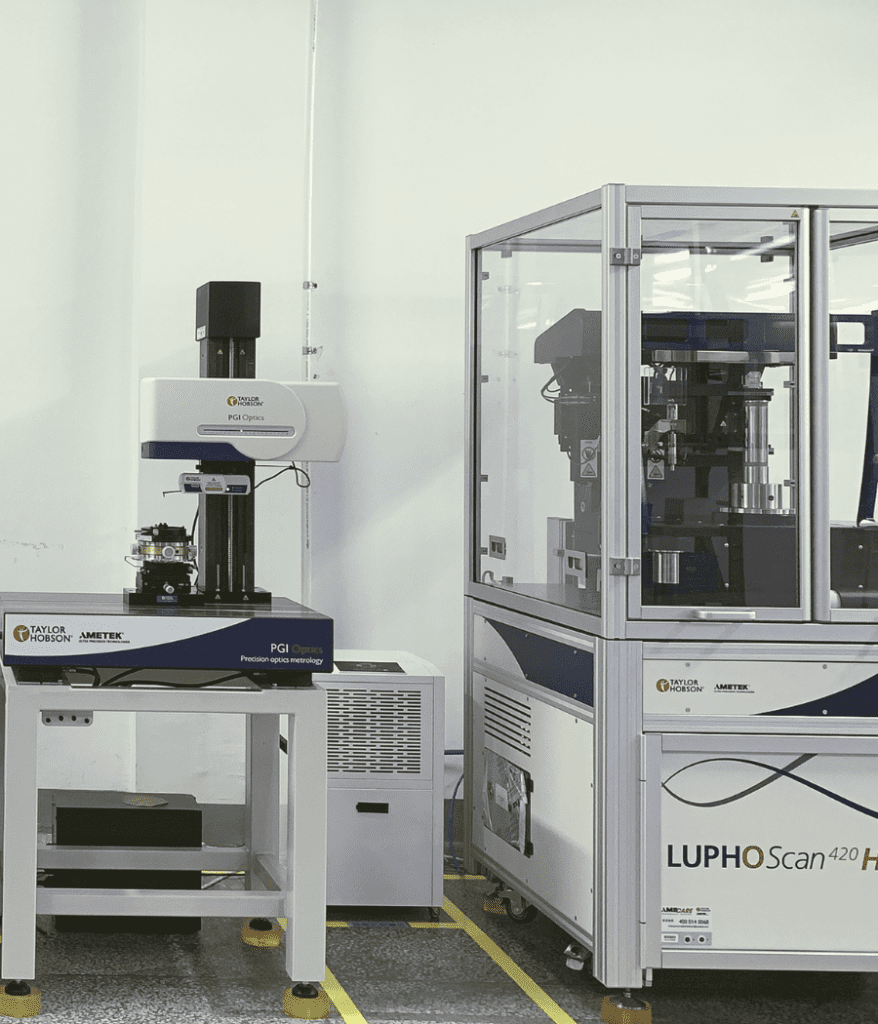
The SpectroMaster® 300 MAN is used to gain an in-depth understanding of the materials used in the original product. As the most accurate refractive index measurement system currently available, it ensures result accuracy and aids in finding suitable substitute or optimized materials.
To measure the spectral properties of optical elements such as transmittance and reflectance, the Agilent Cary 7000 Spectrophotometer and Shimadzu UV3600 Spectrophotometer are utilized. These measurements provide valuable insights into the optical performance and characteristics of the components, facilitating reproduction or improvement of their optical properties.
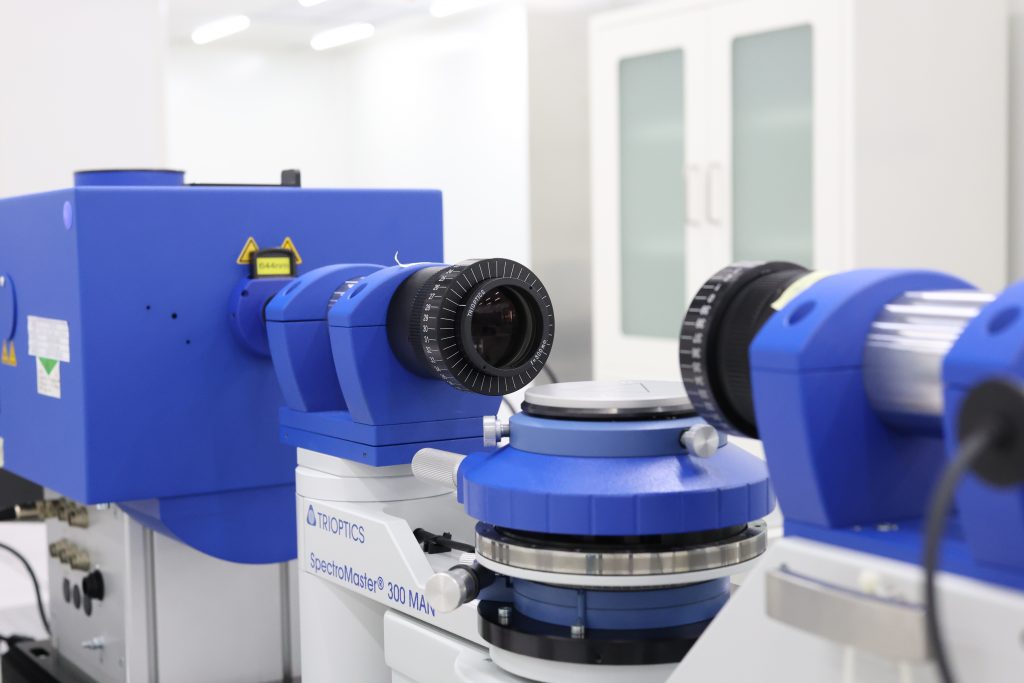
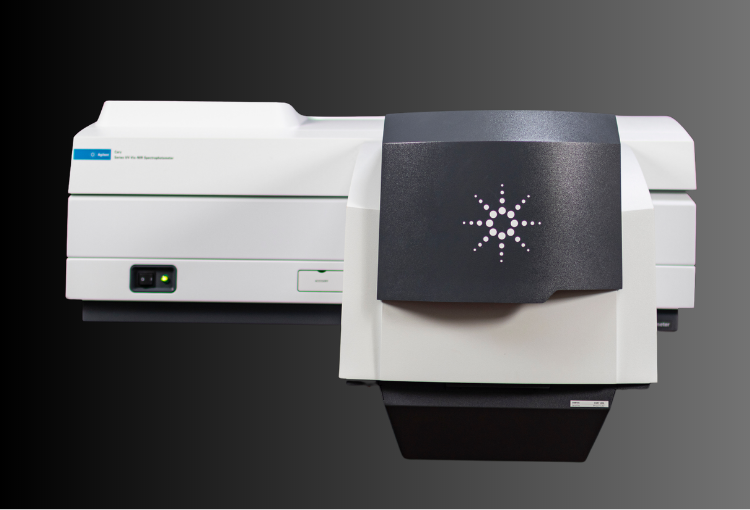
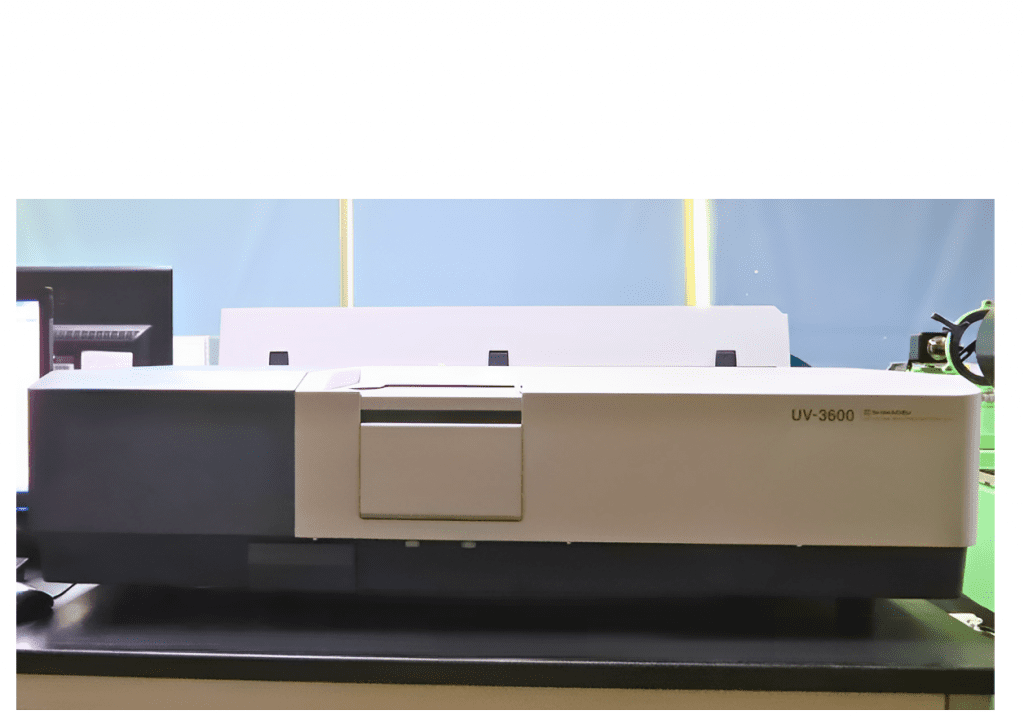
The TriOptics OptiCentric 100 Dual can accurately measure the centration (alignment) of lenses, prisms, mirrors, and other optical elements, assisting in achieving optimal alignment and ensuring the optical system’s best performance and image quality.
For testing the Modulation Transfer Function (MTF), which is one of the measurement parameters used to evaluate the imaging performance and quality of optical systems, particularly lenses, the TriOptics MTF Test Stations and Optical System Testing are employed. Once the measurements are complete, the elements/systems can be further optimized based on the acquired data if required.
AutoCAD software is used to create a virtual model of the product or system based on the acquired measurements and data. Zemax software is utilized for optical and illumination system design, analysis, and optimization.
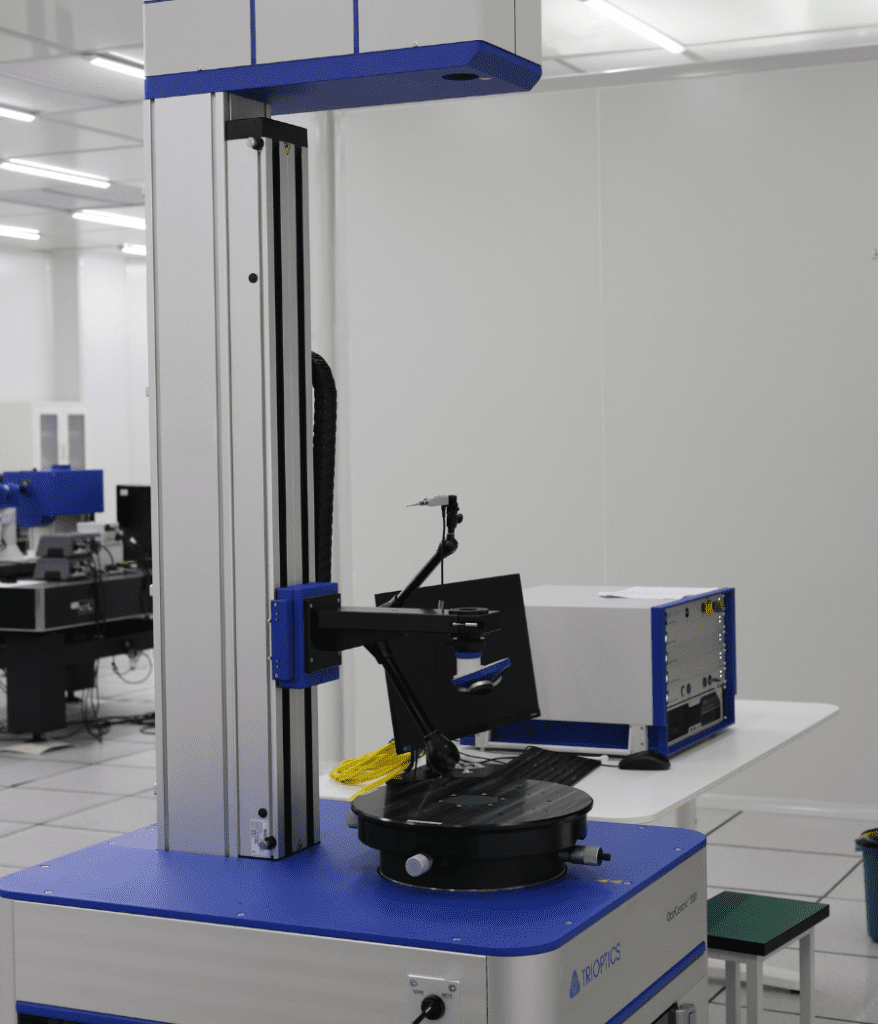
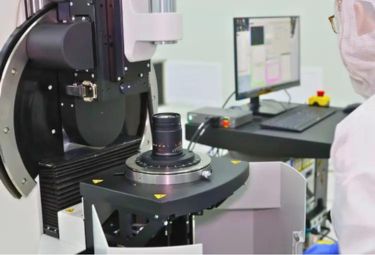
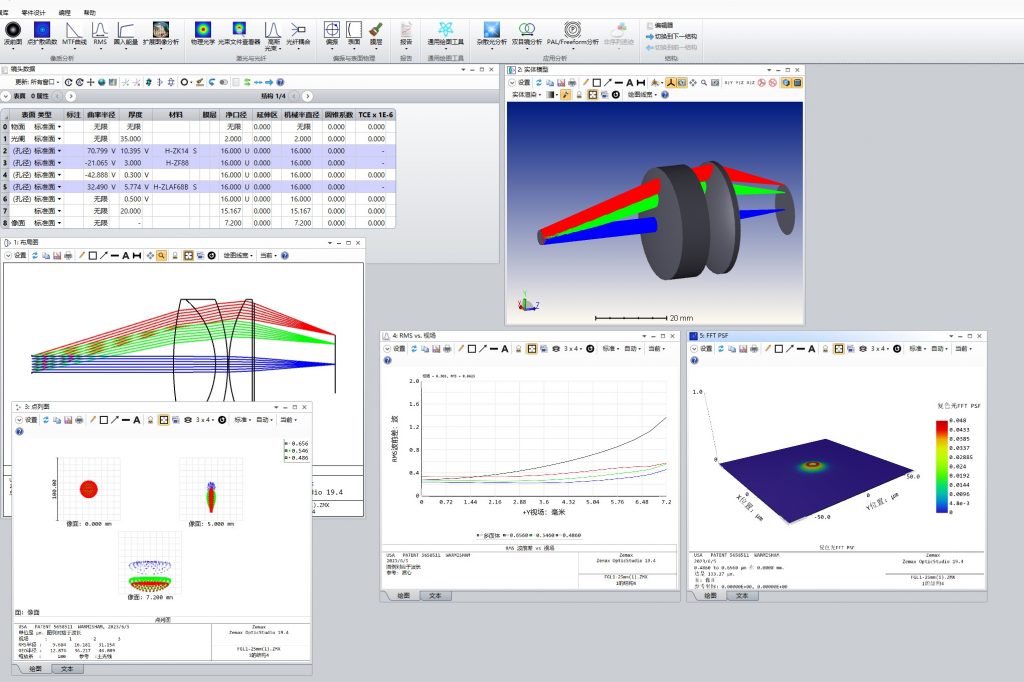
Reverse optical engineering processes in the field of optical engineering utilize various techniques and tools. Advanced metrology instruments like coordinate measuring machines (CMMs), interferometers, profilometers, and spectrophotometers are employed to capture precise geometrical features, measure surface quality, assess roughness, and analyze spectral characteristics of optical components. These metrology tools provide engineers with accurate data necessary for reverse engineering.
Furthermore, the integration of Modern Technologies and Gadgets (MTG) has significantly advanced the field. Sophisticated imaging technologies like 3D scanners and digital microscopy enable engineers to capture high-resolution images and precise measurements, enhancing the accuracy and efficiency of the process. Additionally, cutting-edge software tools, particularly Computer-Aided Design (CAD) software, are utilized to create digital representations of optical components, facilitating analysis and modification of design parameters.
The process of reverse optical engineering is a comprehensive undertaking that combines optical engineering expertise with precision metrology. Engineers meticulously analyze and interpret the data obtained from metrology instruments to gain insights into the existing optical design and manufacturing processes. This knowledge serves as the foundation for recreating or modifying the optical component or assembly, ensuring that the resulting product meets the desired specifications.
Avantier, a trusted provider of reverse engineering services, offers a comprehensive range of solutions tailored to the specific needs of the optical industry. Whether you require dimensional analysis, optical testing, or detailed documentation, Avantier can provide you with the expertise and support you need. Contact Avantier for more information and to discuss your specific reverse engineering requirements.
WE CAN HELP YOU!
Contact us NOW for sales & expert advice.