Key Takeaways
- Silicon carbide optics (SiC optics) are increasingly popular in semiconductor, aerospace, astronomy, and laser applications due to their high thermal stability, low density, and excellent thermal conductivity.
- SiC Optics’ ability to be shaped into various forms and its high specific stiffness make it an ideal substrate.
- Different types of SiC, like reaction bonded, sintered, and CVD SiC, each have unique properties influencing their performance and manufacturing complexity.
- Understanding these differences is crucial for optimal use. Properly manufactured SiC can greatly enhance optical applications, while poor quality can be detrimental.
Silicon Carbide Optics
There’s a reason that silicon carbide optics are becoming more and more prevalent in the semiconductor industry as well as in aerospace, astronomy, and high energy laser applications. If you work with high temperatures or in thermally variable environments, it’s a substrate you don’t want to miss.
SiC is a non-toxic material, and it can be formed into almost any shape desired. It has low density, a low coefficient of thermal expansion and excellent thermal stability, and it also has high specific stiffness and some important resonant frequency advantages. It can transmit heat a hundred times faster than glass, and exhibits more than four times the resistance to gravity deformation. What’s not to like about silicon carbide?
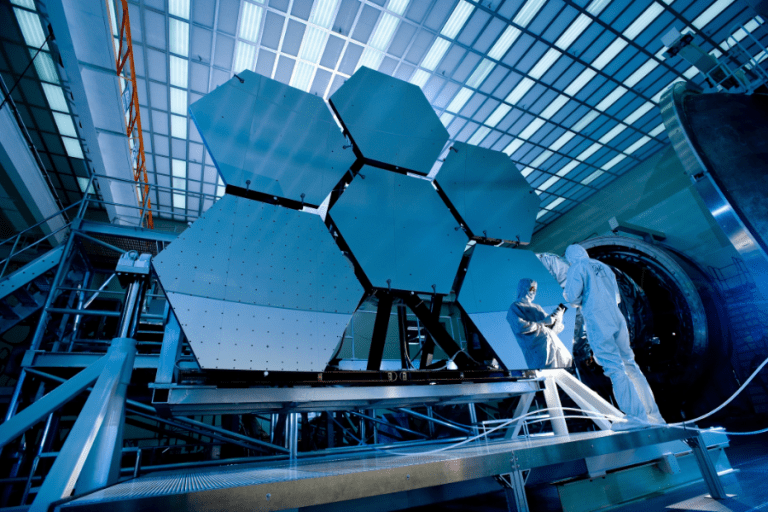
It turns out that though silicon carbon is ideal for many optical applications, it requires a knowledgeable user to make the most of it. There are many different types of silicon carbide, each with its own unique properties. In fact, silicon carbide exists in nearly 250 crystalline forms. Strength, stress, density, and other design parameters all depend on the manufacturing process, as do cost and production lead times. Understanding the nuances of silicon carbide optics and how they are manufactured is important to ensure top performance in your optical application, whether that’s in industry, research, or defense.
This article will introduce you to several different manufacturing processes used to produce this high-performance substrate. Silicon carbide SiC could well be the optimal choice for your application— when it’s done right. Done wrong, it could be little more than a liability.
Types of Silicon Carbide for Optical Use
Types of silicon carbide used in optical applications include:
- Reaction bonded SiC
- Sintered SiC
- 3D Printed SiC
- Hot press sintered SiC
- Reaction sintered SiC
- CVD SiC
- Converted SiC
The table below demonstrates how the properties of silicon carbide depend on manufacturing methods. A single parameter—- specific stiffness vs. thermal stability— is shown for several types of SiC and a number of other popular optical substrates.
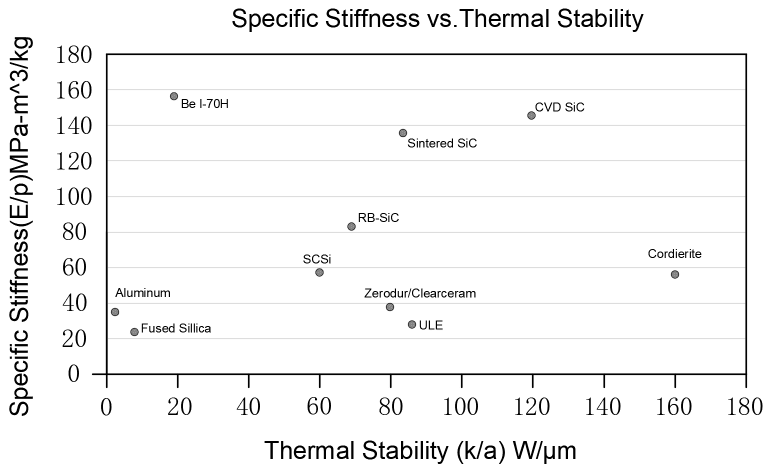
In some optical components, a combination of silicon carbide types may be utilized. For instance, chemical vapor deposition (CVD) results in a form of SiC that can be polished to a significantly smoother finish compared to sintered or reaction bonded SiC. Consequently, CVD SiC may be deposited as a cladding over sintered or reaction bonded SiC substrates to achieve both structural integrity and superior surface quality.
Applications of SiC Mirrors
Silicon Carbide (SiC) mirrors are a prominent type of SiC optics, with several general applications:
1. Space-Based Optical Systems
SiC mirrors are utilized in space telescopes, such as the Herschel Space Telescope, because of their high stiffness-to-weight ratio and low coefficient of thermal expansion (CTE). They are essential for imaging systems in satellites, ensuring precision despite extreme temperature variations.
2. High-Power Laser Systems
These mirrors are employed in beam steering and laser focusing applications. Their high thermal conductivity allows SiC mirrors to effectively dissipate heat, reducing optical distortions.
3. Semiconductor and Lithography Systems
SiC mirrors are used in extreme ultraviolet (EUV) lithography due to their ability to maintain optical performance under high-energy exposure. They are necessary for fast scanning systems in semiconductor manufacturing.
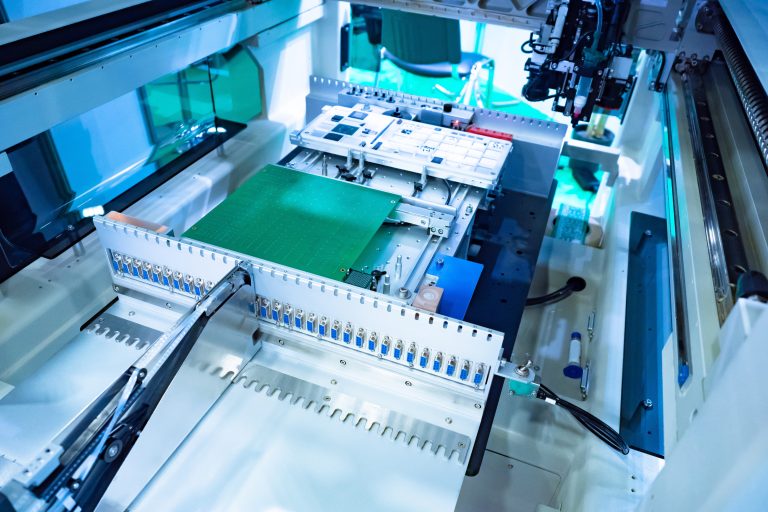
4. Defense and Military Applications
SiC mirrors are applied in infrared (IR) and visible imaging systems for targeting and reconnaissance. They are also used in missile guidance systems where lightweight construction and high thermal stability are crucial.
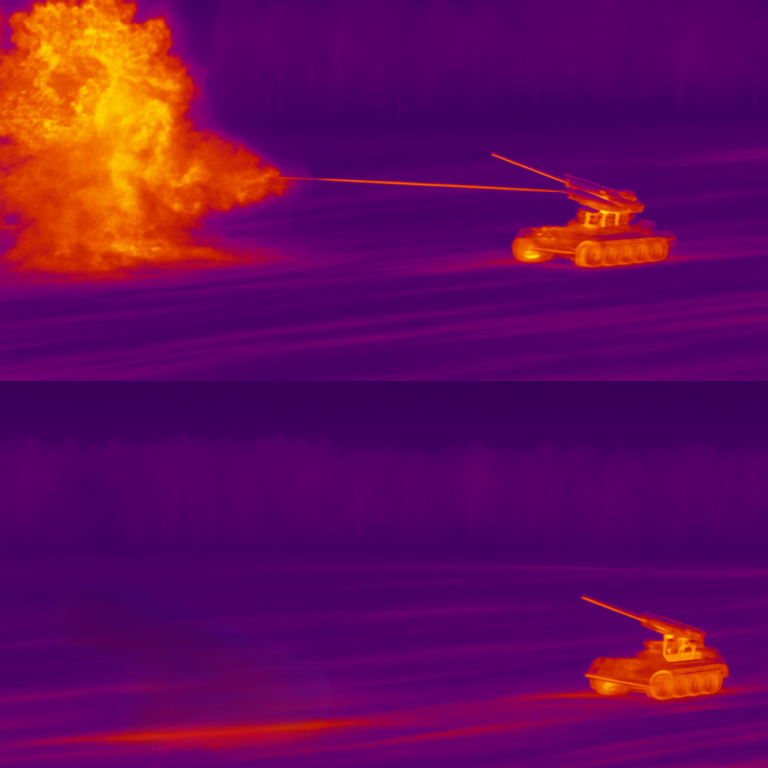
Manufacturing Processes for Silicon Carbide Optics: A Closer Look
Reaction Bonded SiC
Reaction bonded SiC is one popular kind of silicon carbide. Graphite, a plasticizer, and silicon carbide powder are pressed in a preform, and the plasticizer is burned off. The porous structure that results is infiltrated with silicon, which reacts to the carbon (graphite) to form silicon carbide. The substrate that results from this manufacturing process includes residual silicon and carbon as well as silicon carbide. Since there are a number of variables in the process, the quality and mechanical properties of reaction bonded silicon carbide can vary depending on the manufacturer.
Sintered SiC
Sintered SiC is again manufactured from silicon carbide powder, but here heat and pressure is used to form a solid mass. The basic process involves mixing the powder with sintering aids such as carbon and boron, then pressing it into a mold. The powder is then sintered at high pressure and temperatures below the melting point of SiC.
There are a number of variations on the sintering process. Hot press sintered silicon carbide (HIP SiC) uses higher temperatures and pressures to produce a full density silicon carbide. Reaction sintered SiC involves the addition of silicon during the sintering phase, when the materials being processed are at about 1700K. The silicon reacts with 100% carbon used as a sintering aid, and the result is silicon carbide with extremely high flexural bending strength.
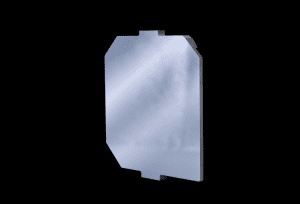
CVD SiC
Chemical vapor deposition is a more expensive technique than either reaction bonding or sintering, but it results in an extremely pure silicon carbide with very good thermal conductivity. The SiC produced by chemical vapor deposition is high density, with a cubic structure, and can be polished very smooth.
To produce CVD SiC, a wafer is heated to a high temperature and exposed to precursors that contain silicon and carbon. These precursors are reduced to form silicon carbide, and by-products are eliminated with the gases.
Manufacturing Challenges of SiC Optics
Producing high-precision SiC optics presents several significant challenges:
- Difficult Machinability: Silicon carbide’s extreme hardness (Mohs hardness ~9.5) makes grinding and milling operations challenging and often necessitates slow and costly diamond cutting techniques.
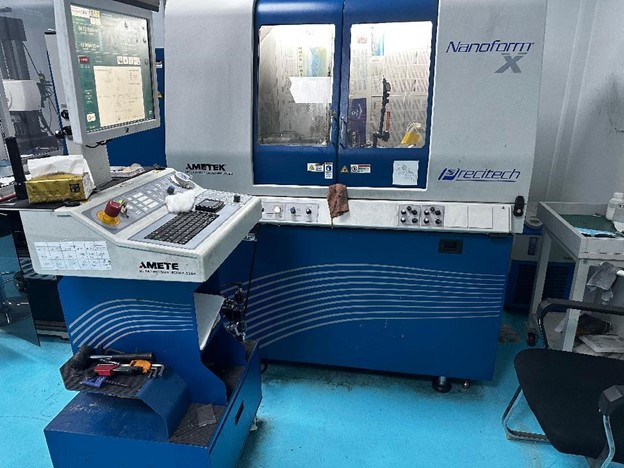
- Achieving Ultra-Smooth Optical Surfaces: The inherent grain structure and potential porosity of SiC can hinder the achievement of ultra-smooth finishes (below 1 nm RMS roughness), often requiring advanced polishing techniques like chemical mechanical polishing (CMP).
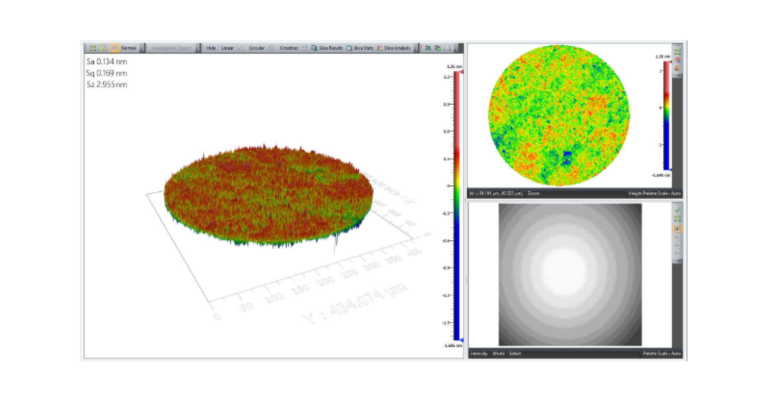
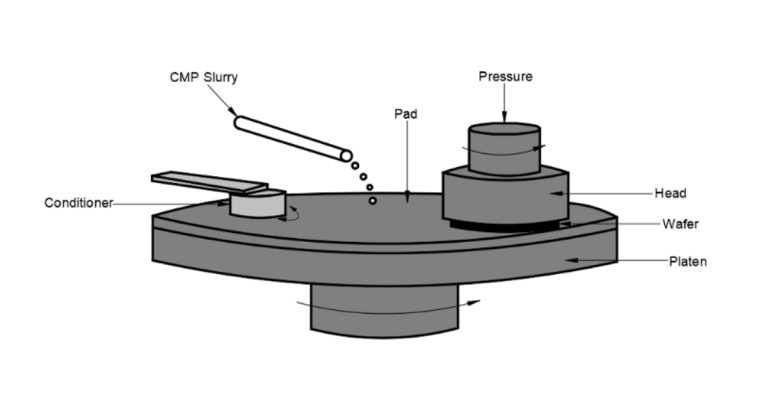
- Thermal Stress and Coating Challenges: Mismatches in thermal expansion between SiC and applied coatings can induce stress and deformation. Achieving uniform reflective coatings often requires sophisticated techniques like ion beam sputtering (IBS).
- Cost and Scalability Issues: The higher cost of raw materials and processing compared to conventional optical materials like fused silica, along with the complexity of fabrication, can limit large-scale production.
Solutions and Advancements in SiC Optics Manufacturing
Despite the challenges, innovative solutions and advancements are continuously being developed:
- Advanced Fabrication Techniques: Techniques like Hot Isostatic Pressing (HIP) are used to improve mechanical strength and surface finish. Variations of CVD are employed to produce high-purity SiC coatings with enhanced polishability.
- Innovative Polishing Techniques: Ion Beam Figuring (IBF) allows for nanometer-scale material removal, achieving high accuracy. Magnetorheological Finishing (MRF) offers non-contact polishing for sub-nanometer smoothness. Chemical Mechanical Polishing (CMP) combines chemical etching and mechanical abrasion for ultra-smooth surfaces.
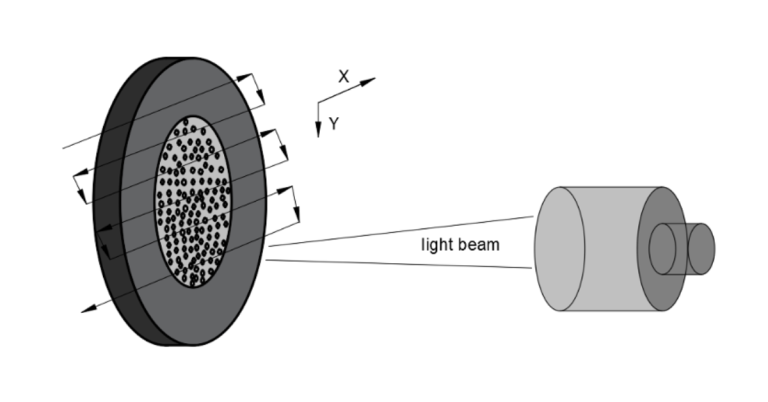
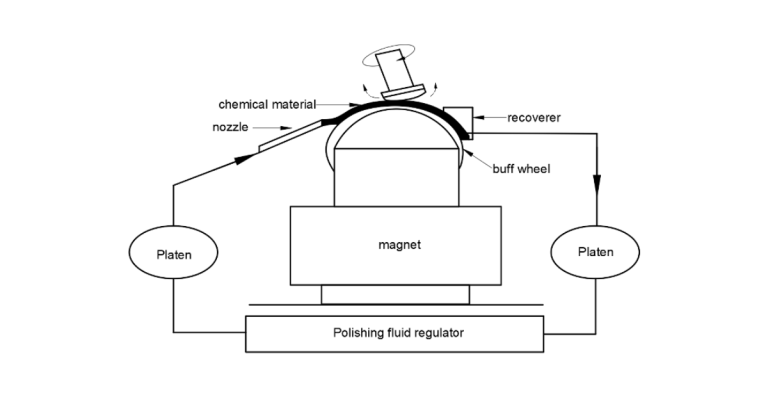
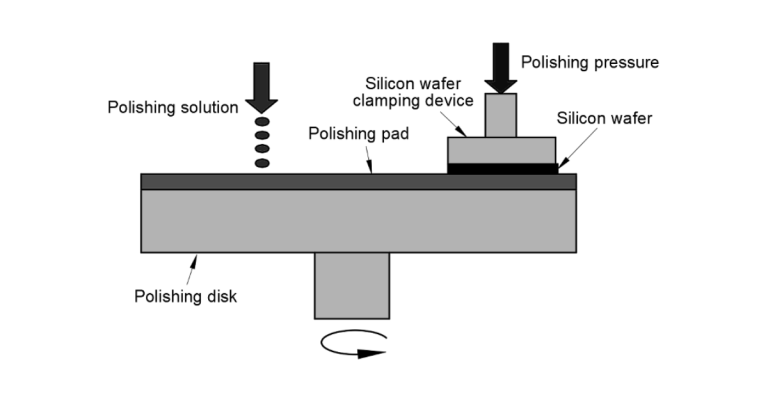
- Thermal and Optical Coating Improvements: Gradient coatings are designed to better match the thermal expansion of SiC, reducing stress. Atomic Layer Deposition (ALD) ensures defect-free and highly uniform coatings. Adhesion layers, such as thin films of chromium or silicon, are used to improve the bonding between SiC and reflective coatings.
- Cost Reduction Strategies: The use of hybrid materials, combining SiC with lighter and potentially less expensive materials like carbon composites, can help reduce overall cost. Additive manufacturing (3D printing) techniques are emerging as a cost-effective way to fabricate complex SiC shapes.
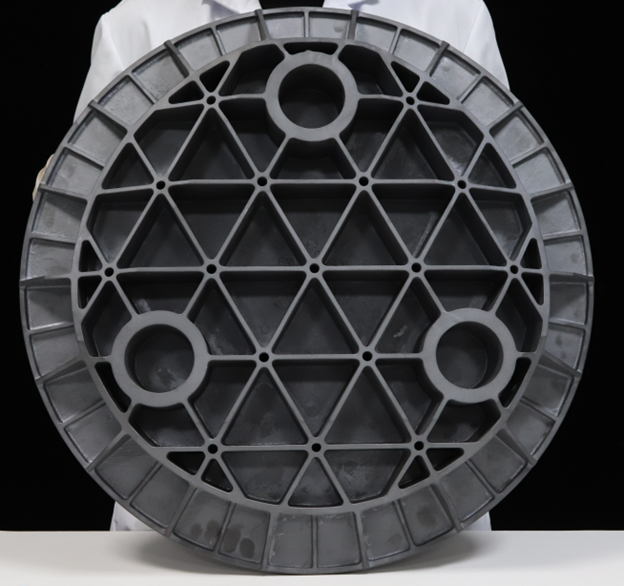
SiC Optics at Avantier
Silicon carbide mirrors are essential in modern optics, providing exceptional performance in extreme environments. Although there are significant challenges in their fabrication, advancements in polishing, hybrid designs, and coating techniques have enabled SiC mirrors to excel in demanding applications such as space exploration and semiconductor lithography.
As additive manufacturing and surface engineering continue to progress, SiC mirrors are anticipated to play an even greater role in next-generation optical systems, opening up new possibilities in aerospace, defense, and photonics.
At Avantier, we design and produce custom high performance SiC optics for clients in many fields. Visit our product page for more info, or contact us to discuss your next project.
GREAT ARTICLE!
Share this article to gain insights from your connections!