Key Takeaways:
- Manufacturing space gravitational wave telescopes, like the Engineering Development Unit Telescope and the Laser Interferometer Space Antenna (LISA), requires extreme precision, advanced materials, and innovative systems to detect gravitational waves.
- Key challenges include producing high-precision optical components, developing radiation-resistant materials, and maintaining ultra-stable laser systems.
- Inter-spacecraft alignment and environmental durability are crucial for performance, especially under harsh space conditions.
- Costly manufacturing processes and complex supply chains complicate production, but recent solutions such as additive manufacturing, active optics, and advanced metrology help overcome these challenges.
The Challenges of Manufacturing Space Gravitational Wave Telescopes
The Engineering Development Unit Telescope arrived at Goddard Space Flight Center in May 2024. This prototype was manufactured and assembled by L3Harris Technologies in Rochester. The primary mirror is coated in gold to reflect the infrared lasers and reduce heat loss from exposure to cold space, allowing it to operate optimally near room temperature. This development marks a significant advancement in astrophysical observations and cosmological studies.
Space gravitational wave telescopes, such as the Laser Interferometer Space Antenna (LISA), are designed to detect minuscule ripples in spacetime caused by gravitational waves. LISA, set to launch in the near future, will use a constellation of spacecraft spread over millions of kilometers to form a sensitive laser interferometer in space. This innovative approach enables unprecedented precision in measuring these ripples, requiring extreme stability and durability in space’s harsh environment. The advancements in LISA’s technology and engineering serve as a reference point for developments like the Engineering Development Unit Telescope, emphasizing the importance of sophisticated systems capable of operating in near-perfect isolation from external vibrations.
As highlighted, the development of space gravitational wave telescopes is a monumental undertaking, requiring extreme precision, durability, and stability to function effectively in space’s demanding environment. Below, we explore the primary challenges involved in their manufacturing:
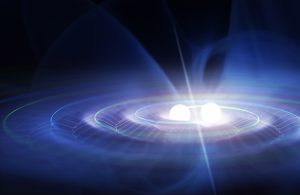
1. High-Precision Optical Components
- Surface Accuracy: Telescope mirrors and lenses require nanometer-scale surface smoothness to minimize phase noise and optical distortion. Achieving such precision is a complex and labor-intensive process.
- Wavefront Aberration: To preserve wavefront integrity, optics must be fabricated with sub-wavelength tolerances. This demands meticulous attention to detail and cutting-edge technology.
- Large-Aperture Telescopes: Large apertures are necessary to transmit and receive laser beams across millions of kilometers. Achieving a lightweight yet precise optical assembly is a significant challenge.
2. Material Challenges
- Low Thermal Expansion Materials: Space environments experience dramatic temperature fluctuations, making it essential to use materials with minimal thermal expansion. A glass ceramic called Zerodur, along with options like ULE (Ultra-Low Expansion glass) or silicon carbide, provides the necessary stability. However, processing and shaping these materials remain a notoriously difficult challenge.
- Radiation Resistance: Components must endure cosmic radiation without degrading in performance. Advanced coatings and materials that can withstand long-term exposure are required.
- Drag-Free Test Masses: Test masses, often made of ultra-high-density and purity materials like gold-platinum alloys, must serve as inertial references. Manufacturing these to exact specifications is extremely challenging.
3. Ultra-Stable Laser Systems
- High-Purity Lasers: These telescopes rely on lasers with extremely narrow linewidths and unparalleled stability over long durations. Developing and maintaining such lasers is an intricate process.
- Frequency Stabilization: Stabilizing laser frequency to picometer-level precision requires complex cavity and modulation systems. Miniaturizing these systems for space use adds another layer of complexity.
4. Inter-Spacecraft Alignment
- Long-Distance Beam Steering: Aligning laser beams between spacecraft separated by millions of kilometers requires precise beam-directing systems and rigorous calibration.
- Pointing Stability: Maintaining nanoradian-level pointing accuracy demands highly stable and responsive control mechanisms to counteract dynamic orbital conditions.
5. Environmental Durability
- Thermal Control: Space telescopes must withstand a wide range of temperature gradients. Advanced thermal management systems are essential to prevent expansion or contraction of optical elements.
- Mechanical Vibrations: Vibrations during launch pose significant risks to delicate optical systems. Shock-absorbing designs and materials are critical for protection.
- Contamination Control: Dust, outgassing, and other contaminants can severely impact optical performance. A clean environment during assembly and operation is crucial.
6. Integration of Drag-Free Systems
- Free-Floating Test Masses: Test masses must be isolated from all contact with surrounding structures. Minimizing stray forces, such as electrostatic fields or thermal gradients, requires precise engineering.
- Electrostatic Positioning: High-precision sensors and actuators must maintain the test masses in perfect free fall without perturbation, demanding exceptional design and integration accuracy.
7. Large-Scale Assembly and Testing
- Ground Testing Limitations: Simulating zero gravity and long-baseline interferometry on Earth is practically impossible. Innovative testing setups are required to approximate space conditions.
- System Integration: Aligning optical, mechanical, and electronic components with high precision during assembly is an intricate and demanding task.
8. Cost and Scalability
- High Manufacturing Costs: Advanced materials, nanometer-scale fabrication, and rigorous testing processes make these telescopes exceedingly expensive to produce.
- Complex Supply Chains: Specialized components and precision manufacturing often involve multiple industries and countries, complicating logistics and increasing costs.
Examples of Recent Solutions
- Additive Manufacturing: Enables the production of lightweight, complex structures with precise tolerances.
- Active Optics: Adaptive systems compensate for residual aberrations in real time, improving overall performance.
- Advanced Metrology: High-precision interferometers and wavefront sensors are used for testing and aligning components, ensuring unparalleled accuracy.
Overcoming Challenges of Manufacturing Space Gravitational Wave Telescopes
The challenges of manufacturing space gravitational wave telescopes highlight the intersection of cutting-edge technology and engineering ingenuity. By overcoming these obstacles, scientists and engineers are paving the way for groundbreaking discoveries in astrophysics, bringing us closer to unraveling the mysteries of the universe.
GREAT ARTICLE!
Share this article to gain insights from your connections!