Key Takeaways:
- Athermal Design ensures stable performance of athermal optical systems across a wide temperature range.
- Athermalization techniques minimize the impact of temperature fluctuations on imaging quality.
- Careful material selection and advanced optical design are crucial for successful athermalization.
- Athermal optical systems find applications in diverse fields, including aerospace, defense, and medical imaging.
Athermal Optics Masters Temperature Challenges
Athermal optical systems are engineered to maintain consistent performance across a wide range of temperatures without the need for active thermal compensation. This is crucial for applications like aerospace, defense, and outdoor imaging where environmental conditions can fluctuate dramatically. By eliminating the need for complex thermal controls, athermal designs offer enhanced reliability and performance under extreme conditions.
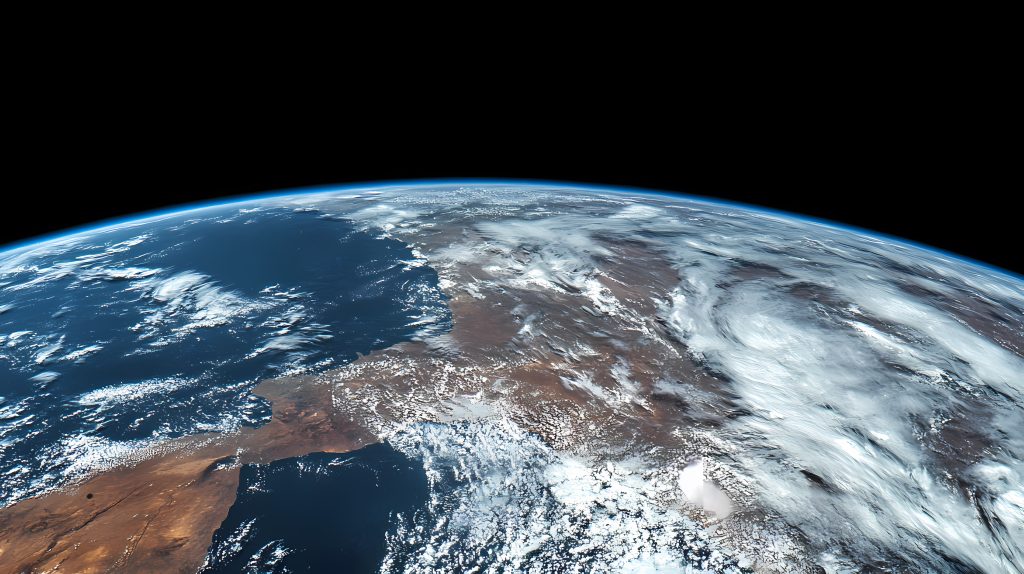
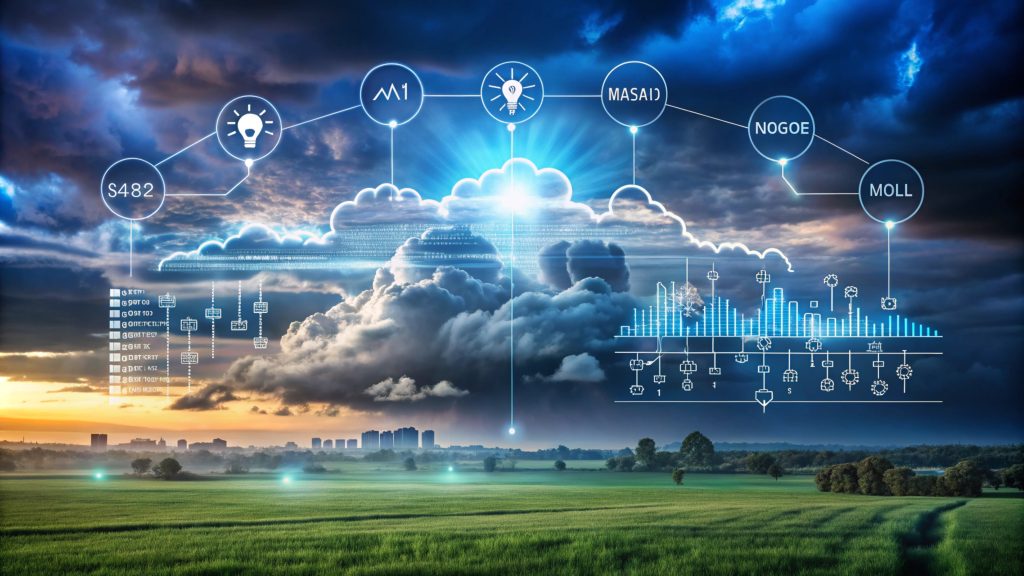
Key Characteristics
- Passive Thermal Compensation: Athermal systems utilize materials and configurations that automatically adjust to temperature-induced changes, ensuring stable optical performance.
- Wide Temperature Range: These systems operate efficiently across a broad temperature spectrum, typically from -40°C to +80°C or more.
- Material Selection: Careful selection of materials with specific thermal expansion coefficients (CTE) and refractive index temperature dependencies is essential for maintaining optical stability.
Athermal Design Principles
When designing an athermal optical system, both application-specific requirements and general athermalization techniques must be kept in mind. Some important aspects of athermal design include:- Thermal Compensation: Athermal designs combine materials with complementary thermal properties. For example, high dn/dT (refractive index change with temperature) materials like Germanium are paired with low dn/dT materials such as Zinc Sulfide or Calcium Fluoride to balance thermal-induced focal shifts. To maintain system effectiveness over a wide range of wavelengths, only substrates which stay transparent over the entire relevant temperature range may be used.
- Optical Layout: Advanced optical components like achromatic doublets and aspheric surfaces are employed to counteract thermal effects and enhance overall performance.
- Mechanical Design: Low-expansion alloys like Invar are used for mounts and housings to minimize distortion and prevent misalignment due to temperature variations.
Design Process
Some processes important to the design of athermal design include:- Temperature Modeling: Advanced simulation software is used to model temperature effects on optical performance, allowing designers to anticipate potential issues early in the development process.
- Material Selection: Identifying materials with complementary CTEs and thermo-optic coefficients is crucial for ensuring system thermal stability.
- Athermal Optimization: Software like Zemax or Code V is used to fine-tune the design, optimizing the layout for both performance and manufacturability. Tolerance analysis is also performed to ensure the system meets stringent production requirements.
Manufacturing Considerations
- Material Precision: Materials like Germanium and Zinc Sulfide are sensitive to thermal and mechanical stresses, requiring precise fabrication techniques like diamond turning to maintain high levels of accuracy and minimize defects.
- Coating: Applying anti-reflective (AR) coatings designed specifically for infrared wavelengths (3–5 µm or 8–12 µm) is vital for maintaining performance. These coatings must withstand the stresses of thermal cycling, and may require advanced application techniques to ensure durability and adhesion.
- Lens Surface Quality: Maintaining high-quality lens surfaces is critical. Stringent scratch-dig specifications are enforced to ensure minimal scattering and achieve clear, sharp imaging.
- Mechanical Housing: Housings made from materials like Invar or Titanium, which have low thermal expansion coefficients, are carefully designed to ensure that components remain securely aligned under varying temperature conditions.
- Testing Methodologies: After manufacturing, each athermal system is subjected to thorough testing to ensure it will perform as expected over the entire relevant temperature range.
- Environmental Stress Testing: Thermal cycling tests, which subject the system to temperatures ranging from -40°C to +85°C, simulate real-world environmental conditions. Vibration testing is also conducted to ensure system stability during transportation or deployment in rugged environments.
- Optical Performance Testing: Modulation Transfer Function (MTF) measurements are taken across temperature ranges to verify that the system meets performance standards and that the image remains clear and sharp.
- Coating Verification: The durability and performance of AR coatings are rigorously tested using spectrophotometry to ensure they provide reliable transmission and resist degradation under thermal stress.
- Reliability Testing: Long-term exposure to thermal and mechanical stress is used to ensure the system will maintain its performance and structural integrity over time.
Advantages of Athermal Optics
There are many benefits to using athermal optics when working under high or changing temperatures. A few of them include:- Thermal Stability: Athermal designs ensure that optical systems deliver consistent performance, even in harsh environmental conditions.
- Reduced Maintenance: The passive nature of athermal systems eliminates the need for complex active compensation mechanisms, leading to lower maintenance costs.
- Improved Imaging Performance: By compensating for thermal effects, athermal optics deliver clear, high-resolution images with minimal distortion, even in extreme conditions.
- Compact Designs: Athermal systems can achieve smaller, lighter designs by reducing the number of components, making them more efficient and easier to integrate into various applications.
Challenges
Despite their benefits, developing and deploying athermal optics involve several challenges that require advanced techniques and innovative approaches to overcome:
- Material Machining: The brittleness of materials like Germanium and Zinc Sulfide requires careful machining techniques like diamond turning to minimize damage.
- Coating Application: Ensuring that AR coatings adhere uniformly to the materials is challenging. Advanced deposition techniques are employed to enhance durability.
- Alignment Precision: Achieving perfect alignment during assembly is crucial for system performance. Advanced alignment tools and stress-free mounting techniques are utilized.
- Thermal Stress Management: Managing thermal stress from mismatched CTEs can lead to mechanical issues. Selecting materials with complementary CTEs and using thermal compensators are crucial to high performance in athermal systems.
- Testing and Quality Assurance: Comprehensive testing is resource-intensive. Automating testing processes and implementing rigorous quality control protocols are essential.
- Cost and Scalability: Manufacturing athermal systems can be expensive. Optimizing designs, streamlining processes, and exploring partnerships are crucial to lower costs.
While athermal optics excel at addressing thermal challenges, limitations in material selection, environmental factors, and manufacturing costs underline the importance of balancing their benefits with practical constraints.
Athermal Optics for Superior Imaging
Athermal optics are a transformative technology, ensuring that optical systems perform reliably across a wide range of environmental conditions, from extreme heat to freezing cold. Through careful material selection, innovative design principles, and advanced manufacturing processes, athermal systems meet the demanding needs of industries ranging from aerospace to thermal imaging systems to medical and automotive. Contact us on your athermal optics project.
Related Content
GREAT ARTICLE!
Share this article to gain insights from your connections!