Key Takeaways
- This Aspherical Lenses Reverse Engineering case study details the reverse engineering of a double aspherical lens used in laser cutting systems.
- By precisely measuring geometry, modeling surface equations, and analyzing material and coatings, Avantier reduced R&D time by over 60% and cut costs by 50%.
- Advanced tools like interferometers, profile meters, and Zemax simulations ensured accuracy.
- The process lends itself to technical innovation, IP protection, and rapid, cost-effective replication—ideal for industries like laser processing, semiconductors, and aerospace.
Analysis of Aspherical Lenses Reverse Engineering
Background: As a core component of high-precision optical systems, aspherical lenses effectively address traditional spherical aberration issues through their unique curved surface design and superior optical performance. They offer distinct advantages, such as improved focusing efficiency and optimized light speed quality.
In today’s rapidly evolving technological landscape, companies must continuously innovate and upgrade their products to enhance performance and reduce costs. Conducting reverse engineering allows them to analyze advanced technologies, providing key information for their own product development. Reverse engineering may also help strengthen intellectual property protection and prevent infringement.

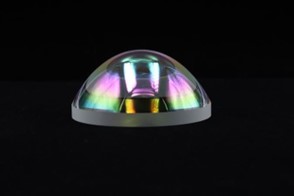
Case Analysis of Reverse Engineering of Aspherical Lenses
One example of reverse engineering at Avantier is a recent challenge we took on to reverse engineer an aspherical lens for industrial use. Our team conquered significant challenges to produce a high-quality double aspherical lens that functioned as desired. The new lens was the perfect match for the original, from geometric parameters to reflective coatings.
Lens Features: Double aspherical lens
Application: High-power industrial flat panel laser cutting machine
- Reverse Engineering Challenges: The surface sag of aspherical lenses does not follow a regular pattern. During manufacturing, processing must adhere to the sag formula. In the absence of design documents, it becomes extremely difficult to understand detailed formula parameters, especially those related to higher-order aspherical formulas.
- Generally, to obtain these parameters through reverse engineering, one must first test the actual sag of the asphere. Software is then used for analysis and fitting to derive accurate parameters. For a higher-order even-order aspherical lens, the goal of reverse engineering is to accurately obtain the vertex radius of curvature, k value, and the values of each order term in the formula.

Reverse Engineering Steps:
1. High Precision Geometric Parameter Measurement: In the first step, geometric parameters are measured with high precision.
- Core Equipment: Three-coordinate measuring machine (precision ±1μm), optical profiler, ZYGO laser interferometer
- Technical Highlights: Full-size coverage, accurate acquisition of basic parameters such as lens outer diameter, vector height, and center/edge thickness.
2. Aspheric Surface Modeling and Equation Fitting: When measurements are complete, specialized equipment and software are used for aspheric surface modeling and equation fitting.
- Technical Difficulties: Aspherical equations are complex; high-order coefficients are difficult to measure directly and need to be deduced from the actual contour.
- Solution:
- High-Density Point Cloud Scanning: The lens surface is scanned with a Taylor Hobson profile meter at nanometer precision, generating millions of data point clouds.
- Intelligent Parameter Reverse Inference: The aspheric equation is fitted using professional software (e.g., TalyMap). An optical simulation done with Zemax ensures that the error between the theoretical surface shape and the actual profile is less than 0.1%. The figure below shows the vector height obtained by analyzing a lens object with different contour meters. It is assumed that the aspheric surface uses 16 parameters derived by professional engineers through precise testing and software. The analysis shows that the test parameters obtained from different devices are very similar.
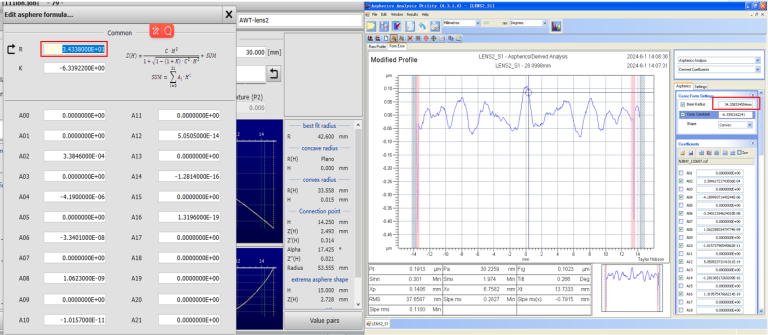
3. Lens Material and Coating Information Analysis
In this step, the refractive index and Abbe coefficient of the lens are rapidly analyzed using an Abbe refractometer and spectrometer to determine the material types. This test is destructive and is usually conducted at the end of the reverse engineering process. The reflectivity of the lens film layer is accurately measured with a reflectivity meter, and a film system with a similar anti-reflection effect is designed.
Customer Benefits: Avantier’s reverse engineering process results in some significant customer benefits:
- Cost Reduction and Increased Efficiency: With reverse engineering, the cycle is shortened by over 60%, and we can go from sample testing to parameter delivery in just 7 days. Costs are reduced by over 50%, enabling competitive procurement and significantly lowering supply chain costs.
- Technological Breakthrough: Companies can increase their efficiency and incorporate innovations easily.
Advantages of Avantier’s Reverse Engineering
Why choose Avantier for your reverse engineering needs? Here are a few reasons:
- Equipment Matrix: We have a full range of technical tools available, including nanoscale measurement (profilometer), intelligent parameter fitting (TalyMap), and optical simulation (Zemax).
- Industry Experience: Our extensive experience servicing customers in fields such as laser processing, semiconductor lithography, biomedicine, and aerospace ensures that your project will not lack expertise.
- Delivery Assurance: Our one-stop closed-loop solution of “parameter + process + testing” supports a seamless transition to mass production.
Please contact us if you’d like to request a quote on your next project.
Related Content
GREAT ARTICLE!
Share this article to gain insights from your connections!