Key Takeaways
- Metal film coatings for mirrors, including AR coatings and metallic films, enhance reflection.
- AR coatings reduce light reflection on optical materials, improving transmittance.
- Different metal coatings like copper, silver, aluminum, germanium, magnesium fluoride, gold, and chromium have unique applications in optics.
Anti-Reflective (AR) Coatings and Metal Film Coatings for Mirrors
The article has already covered various types of coatings. In this particular piece, our focus will shift towards delving into the specifics of AR coatings and metal film coatings, particularly in the context of mirrors. In this article, we will delve into Metallic Mirror Coatings: The process of applying a thin metal film onto a substrate, such as glass or plastic, enhances its reflective qualities, effectively transforming it into a functional mirror.
Anti-Reflective (AR) Coatings:
AR coatings are thin films applied to the surface of optical materials (glass, plastic, etc.). Its main purpose is to reduce light reflection. Reducing reflections from the surface of the material improves the transmittance and visibility of transparent materials.
How AR coatings work:
Light propagates between different media and may be reflected at the interface. AR coatings utilize the interference effect of light by layering multiple thin films. This creates an effect that cancels out reflections of certain wavelengths of light, thereby minimizing reflections.
Applications:
AR coatings are used in many products such as eyeglasses, camera lenses, LCD displays, solar panels, and lighting fixtures. This reduces unpleasant reflections on the surface of transparent materials and keeps vision clear.
Metal film coating for mirrors:
Metal film coating for mirrors is the process of coating a thin metal film on a substrate such as glass or plastic. This improves the reflective properties and allows it to function as a mirror.
How metal film coating for mirrors works:
The metallic film absorbs light using electronic vibrations and reflects some wavelengths. In a metallic film coating for mirrors, a thin layer of a metal (usually silver or aluminum) that enhances the reflection of light is coated on the surface of the substrate. This metallic layer selectively reflects light, creating a mirror with mirror-like reflective properties.
Application:
Metal film coatings for mirrors are widely used in household and commercial mirrors, car rearview mirrors, telescopes, and optical instruments. By adjusting the thickness and composition of the metallic film, it is possible to create mirrors with high reflective properties in specific wavelength bands.
Difference between a front mirror and a rear mirror
Front and rear mirrors are two types of mirrors used primarily in optical equipment and automobiles. There are several differences between these mirrors.
Figure 1: Capturing the pristine reflection from a First Surface Mirror
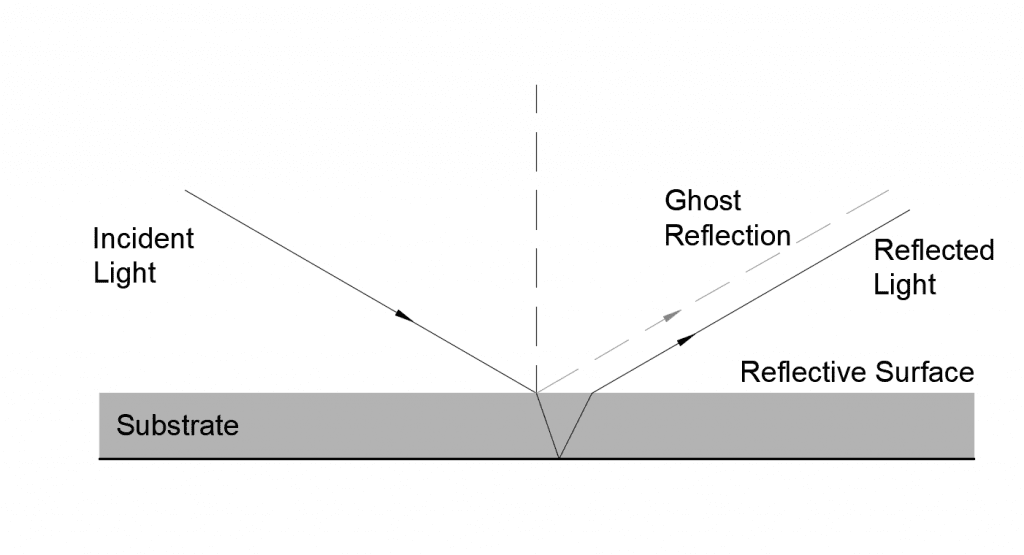
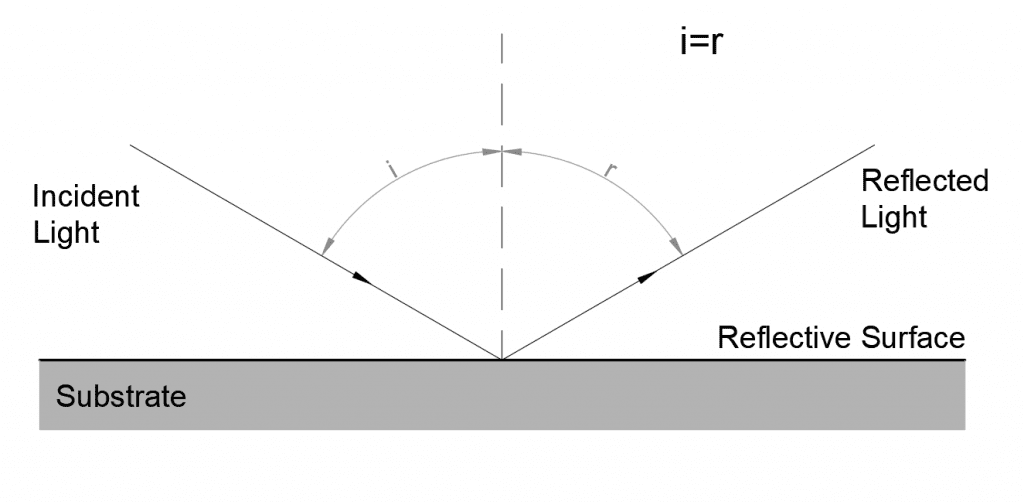
Figure 2: Second Surface Mirror Reflection Revealing Ghost Reflections
and Refraction Within the Mirror Substrate
Front Mirror |
Rear Mirror |
|
Position of reflection |
Light is reflected on the surface of the mirror. The protective or anti-reflective coating on the surface of the mirror is important because light is reflected off the surface of the mirror. |
Light is reflected on the backside of the mirror. Rear-view mirrors are often used in cars to view the rear of the vehicle and provide visibility while driving. |
Differences in visibility |
A front mirror is a common mirror and provides a direct image. The field of view is produced by direct light reflection. |
Rear mirrors use wide-angle lenses or curved mirrors to provide a wide field of view, allowing a wider view of traffic conditions behind the vehicle. |
Coating |
Generally, front mirrors may be coated with an anti-reflective or protective coating. This reduces reflection and scratching and improves the quality of vision. |
Rear mirrors are mainly coated with a metallic film coating. This metallic film coating provides high reflective properties and a bright field of view. |
Because of these differences, front and rear mirrors have different purposes and functions.
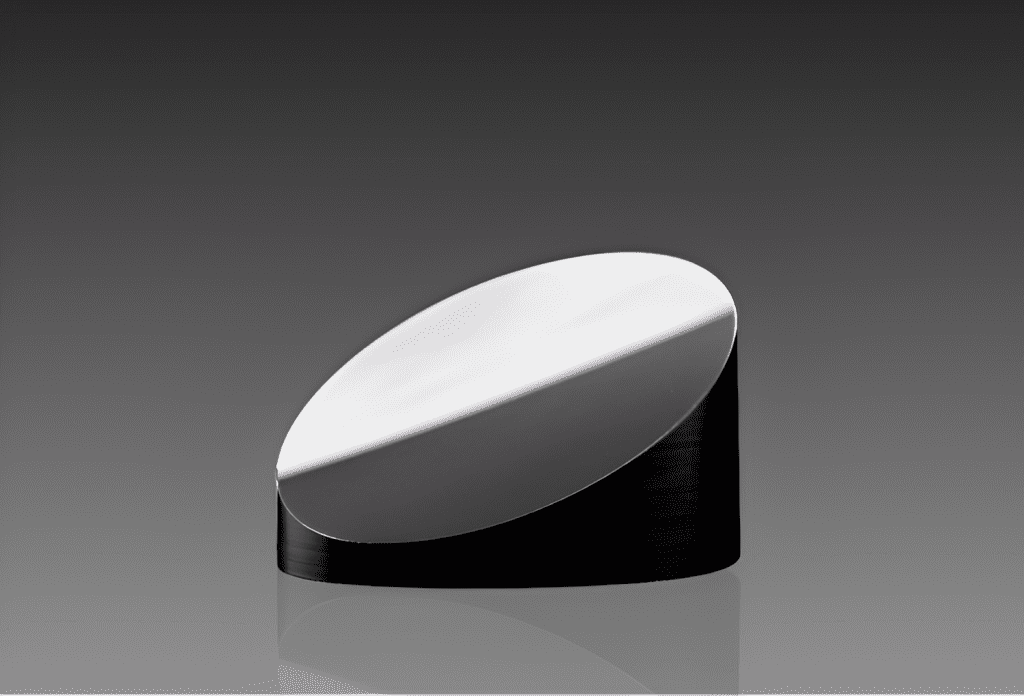
Types of Coatings
We offer coatings in gold, silver, aluminum, chromium, Ge, copper, and MgF2. The characteristics and applications of each metal coating are described below.
Copper
- Copper has high reflectivity over a wide range of wavelengths, but it oxidizes easily and can be more difficult to coat than other metals.
- Applications: Copper coatings are typically used to shield high frequency electromagnetic waves and for communications applications such as RFID antennas.
Silver
- Silver is a highly reflective metal with high reflectivity over a wide range of wavelengths. However, silver is susceptible to oxidation and requires a protective coating.
- Applications: Used in mirrors, optical instruments, optical telescopes and optical lenses. Typically used to coat rearview mirrors.
Aluminum
- Aluminum is lightweight and has high reflectivity over a wide range of wavelengths. It is also a relatively inexpensive metal.
- Applications: Commonly used in surface mirrors, optical lenses, and projector reflectors. It is also sometimes used in optical filters and thin film reflectors.
Germanium (Ge)
- Germanium has high transmission in the near-infrared. It also has a high refractive index and can be used in certain optical devices.
- Applications: Germanium is used as an infrared optical or window material and is suitable for applications such as thermography, spectroscopy, and infrared sensors.
Magnesium Fluoride (MgF2)
- MgF2 is used as a thin film coating and is highly transparent over a wide range from visible to ultraviolet light. It also has effective antireflection properties even in thin films.
- Applications: MgF2 coatings are applied to the surface of lenses and optical instruments to reduce reflections and improve transparency; they can also be used as UV optical materials.
Gold
- Gold has high reflectivity and excellent electrical conductivity. It is also highly reflective over a wide range of visible to near infrared light.
- Applications: It is sometimes used in high-end jewelry, decorative optical instruments and laser optics. It can also be used in biomedical applications such as cell observation.
Chromium
- Chromium has high reflectivity over a wide range of wavelengths. It is also very durable due to its high hardness.
- Applications: Chromium coatings are used in optical filters, mirrors, reflectors and spectrometers. They are also important in a wide range of optical applications due to their high reflectivity at room temperature.
Each of these metal coatings has different properties and applications, and are widely used in optical instruments and other applications. Please refer to the following table for specifications
Material |
Specifications |
Cooper |
Substrate: Fused Silica, H-K9L, etc.Surface Quality: 40-20Chamfer: 0.5mm, 45°Coating Material: Ag, Al, Cr, etc.Clear Aperture: > 90% of diameter |
Silver |
Substrate: Fused silica, BK7Surface Figure: < λ/10 @ 632.8nmSurface Quality: 40-20Chamfer: 0.5mm, 45°Coating Material: SilverClear Aperture: > Central 85% of diameter |
Aluminium |
Substrate: Fused silica, BK7Surface Figure: < λ/10 @ 632.8nmSurface Quality: 40-20Chamfer: 0.5mm, 45°Coating Material: AluminumClear Aperture: > Central 85% of diameter |
Germanium |
Substrate: Germanium, ZnSe, etc.Surface Quality: 40-20Chamfer: 0.5mm, 45°Coating Material: ZnS, YbF3, Ge, etc.Clear Aperture: > 90% of diameter |
MgF2 |
Substrate: Fused Silica, H-K9L, etc.Surface Quality: 40-20Chamfer: 0.5mm, 45°Coating Material: Al2O3, SiO3, HfO2, Ta@O5, etc.Clear Aperture: > 90% of diameter |
Gold |
Substrate: Fused silica, BK7Surface Figure: < λ/10 @ 632.8nmSurface Quality: 40-20Chamfer: 0.5mm, 45°Coating Material: GoldClear Aperture: > Central 85% of diameter |
Chromium |
Substrate: Fused silica, BK7Surface Figure: < λ/10 @ 632.8nmSurface Quality: 40-20Chamfer: 0.5mm, 45°Coating Material: ChromiumClear Aperture: > Central 85% of diameter |
Germanium |
Substrate: Germanium, ZnSe, etc.Surface Quality: 40-20Chamfer: 0.5mm, 45°Coating Material: ZnS, YbF3, Ge, etc.Clear Aperture: > 90% of diameter |
GREAT ARTICLE!
Share this article to gain insights from your connections!