Key Takeaways
- Micro-optics, including lenses used in biomedical sensors and optical fibers, enable advanced miniaturized technologies.
- These tiny components enhance consumer products and biomedical devices with their precision.
- Manufacturing methods include traditional techniques, photoresist reflow, and soft lithography.
- Micro-optics are often integrated into microsystems or produced in arrays for various applications.
The Power of Micro-Optics
Can a lens be mounted on a surface smaller than the head of a pin, or the full power of complex optical devices be condensed into a package smaller than a fingernail? That’s what micro-optics are about.
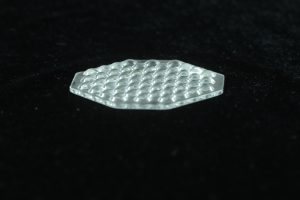
A micro-optic is an optical component or array between a few micrometers and a millimeter in size. These miniature optics are taking an increasingly central position in modern manufacturing as advances in manufacturing make them more accessible to consumer needs. Once the exclusive domain of specialized defense and research projects, cost-effective micro-optics are now to be found in consumer products everywhere, from fiber optical communication systems to smart phones to biomedical devices. Here we’ll look at a few examples.
Biomedical Applications of Micro-Optics
Biomedical sensors are one important use of micro-optics. The core of these sensors is typically a MOEMS, or micro-opto electromechanical system, which incorporates both micro-optics, tiny electronic parts and other mechanical components to create an robust, lightweight system that can be integrated into the human body.
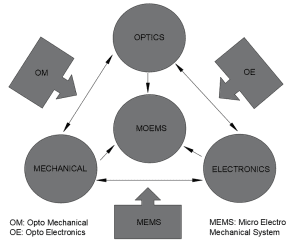
These systems must be carefully manufactured for optimal strength, wear resistance, stiffness, and fatigue resistance. They must also be optimized for their exact function and the environment they will find themselves in the body.
For instance, a 3D intraoral scanner, used within the back, used on photonics MEMS (micro-electronic-mechanical systems) technology can be used to map the 3D image needed for accurate dental restoration. Back pain is difficult to diagnose, but a FBG sensor can be incorporated into the intervertebral disc to provide a better understanding of pressure distribution in the intervertebral disc, and improve clinical diagnostic of disc strain. What about the inner-eye pressure that causes glaucoma? Intraocular pressure build up can be monitored with a micro-sized optical implant using a flexible photonics crystal membrane.
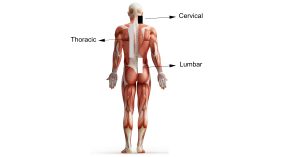
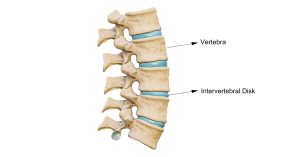
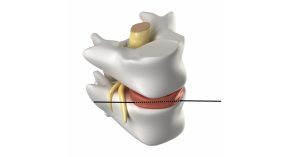
A micro-optic sensor can be used to determine the cause of back problems.
Manufacturing of Micro-Optics
Some micro-optical parts are manufactured in nearly the same way as their non-micro counterparts, though their small size presents unique challenges and requires extra care in manufacturing. The small beam collimator lenses for laser diodes are an example of micro-optics which are usually manufactured with traditional techniques. These tiny lenses may one or two millimeters across.
The ultra-tiny components needed for optical data transmission, though, are not practical to make with traditional methods. A single optoelectronic chip may include microlasers, tiny photodetectors, and a variety of lenses or beam collimators.
One manufacturing method used for these very small micro lenses is called photoresist reflow. A photoresist material is deposited on a circular area with a tiny diameter, typically in the tens of microns. When the device is heated, the photoresist melts. Surface tension gives the melted photoresist a well defined surface with a curvature that is nearly spherical.
Replication techniques such as injection molding, hot embossing, UV casting involve first manufacturing a master structure, then mass producing a large number of identical tiny optics.
Soft lithography, also known as micro contact printing, is another option for microptic manufacture. Here lithograph is applied to optical materials such as a wafer, and surface tension provides the smooth aspheric surface desired. One type of soft lithography is nano imprint lithography (NIL), which uses UV light and special stamps to transfer lens patterns onto prepared optical polymer material. Thousands of lenses can be manufactured on a single 8 inch substrate.
What about if more flexibility is needed? Then direct laser writing may be a possibility. This method can be used to fabricate even complex three dimensional microstructures, and the possibilities it might lead to are currently being explored.
Most of these tiny micro-optics are not usually produced and sold individually. They might be inserted directly into their optical microsystems, which can then be combined into micro-electronic-mechanical systems (MEMS) with unique functions. They can also be produced in the form of one or two dimensional arrays. When necessary, laser-based processes can be used to insert a single microlens on the end of an optical fiber or other micro component.
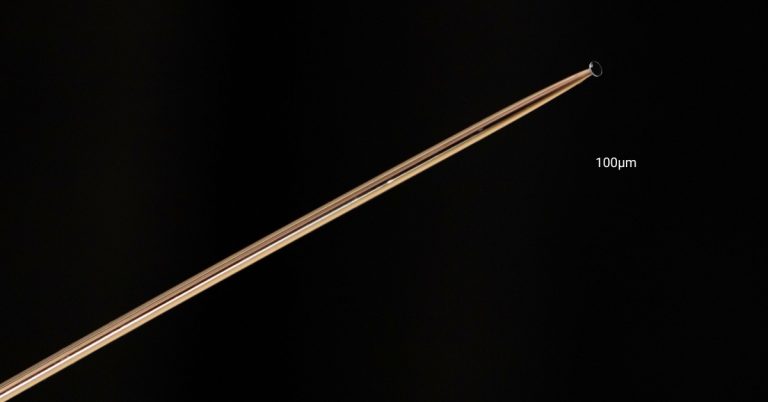
Have we piqued your interest? Contact us today if you’d like to know more about micro-optics and how we can produce custom micro-optics for your application.
GREAT ARTICLE!
Share this article to gain insights from your connections!