Key Takeaways
- Microlens arrays enhance light uniformity in laser, fiber, and other optical systems.
- Fabrication techniques involve photolithography, nano-imprint technology, femtosecond laser direct writing, micro injection molding, and 3D printing.
- Emerging applications include imaging technology, laser processing, biomedical innovation, and autonomous driving.
What if you could bring the power of nature’s compound eyes to your optical assembly— in a tiny package 10 mm x 10 mm? It turns out, you can! Whether you need to homogenize light from line-narrowed excimer lasers or high power LEDS, microlens arrays can give you the high efficiency and non-Gaussian uniformity you need. These optical assemblies are composed of many tiny microlenses, arranged in a one or two-dimensional array.
What is a Microlens Array?
A microlens array is a miniature optical device, typically between several microns to a few millimeters in size, and composed of many even tinier lenses each placed to form a 1D or 2D array on a supporting substrate. Each microlens array may contain thousands or possibly even millions of tiny lenses, arranged to make a square grid, rectangle, or circle. Individually, each lens processes light as does a larger lens, but they also work together to accomplish complex light field regulation.
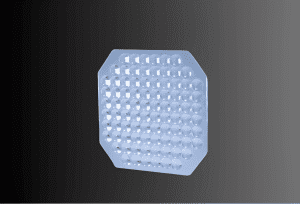
Types of Lens Arrangement in Microlens Arrays
Many of the optical properties of a microlens array will depend on the precise placement of microlenses on the substrate. The fill factor tells us what percentage of a microlens is optically active; i.e., covered by miniature lenses.
Lenses in a microlens array may be close packed or arranged with gaps, depending on the application. The larger the fill factor of a given microlens array, the higher its transmission rate, and the lower the number of zero-order hotspots. But not every pattern is equally suited to each application. Commonly used distribution patterns include:
- A rectangular grid arrangement, similar to a checkerboard. This type of distribution pattern allows for alignment with the grid-like pixel array of electronic sensors.
- Hexagonal close-packed provides the highest fill factor for circular micro-lenses (assuming no overlap).
- Radial gradient distribution; a non-uniform distribution in which the size and/or spacing changes as one moves from the center to edge of the array. This type of distribution can be helpful in eliminating edge distortion and may be used to generate annular beams.
- Randomized distributions of lenses may be used to suppress speckle noise. A randomized arrangement is sometimes used in holographic technology or with laser displays.
Microlens arrays may be produced as separate optical components, or in mounted form, surrounded by metal or polymer that enables them to fit neatly into an optical mount. They can also be designed to incorporate directly into a larger optical system.
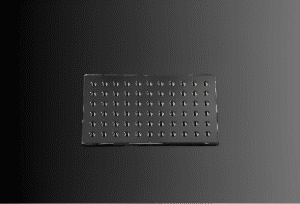
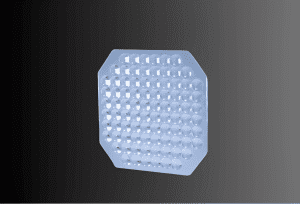
Classification of Microlens Arrays
It can be characterized by parameters such as focal length, quality of transmitted wavefront, and size. They can also be categorized by optical principles, material type, or functional form as well as by distribution pattern.
Classifying by Optical Principles
When classifying by optical principles, we can categorize a microlens array as either refractive, diffractive, or hybrid.
- Diffractive Array: A diffractive array is based on the diffractive principle, specifically, the diffraction and interference that occurs when light passes through the microlens. Diffractive arrays are used to create precision light distribution patterns for fields like optical communication.
- Refractive Array: A refractive array works by bending light toward a material with a higher refractive index, and is primarily used in beam transformation and shaping.
- Hybrid Array: Hybrid microlens arrays use both refractive and diffractive principles and can be used for both focusing and splitting light.
Classifying by Material Type
Many of the properties of a microlens array depend on the materials used. Common choices are glasses, polymers, and semiconductors, and they all have their own strengths and weaknesses.
- Glass-based arrays are characterized by a long lifespan and high temperature resistance. They have versatile optical properties and are a good choice for use in harsh environments. Many microlens arrays are made of UV fused silica, a type of glass that has high transmission from the UV into the IR range.
- Polymer-based arrays are economical to produce and flexible. Though they do not have the temperature or abrasion resistance of glass they are resistant to shock damage. Polymer based arrays are often used in consumer products, where the low price point outweighs any other considerations.
- Semiconductor-based arrays are designed for photoelectric integration, and they can be embedded on a sensor surface on an electric chip.
Classifying by Functional Form
Fill factor and distribution pattern are only part of the functional form of a microlens array. The lenses may take any of a number of geometrical forms. Three of the most common are spherical, cylindrical, and aspheric.- A spherical lens array is the classic standard, most often used for focusing applications. While a square-packed array of spheres has a fill factor of only about 78.5%, hexagonal close packing can bring this above 95%.
- A cylindrical lens array may consist of a stack of dual-surface cylindrical microlenses; this is called a fly’s eye condenser array and has important applications in medical laser, semiconductor instrumentation, solar simulation, and fluorescence microscopy.
- Aspheric lens arrays may be used to improve image quality by eliminating spherical aberration.
Manufacturing a Microlens Array
Fabricating a microlens array is very different from traditional lens manufacturing, and requires skill, careful attention to detail, and specialized equipment. Typically, all of the microlenses in a microlens array are produced in just one step, and the manufacturing methods used are often adapted from semiconductor processing technology.
Photolithography, nano-imprint technology, laser direct writing, micro injection molding, and 3d printing are five methods used to produce microlens arrays.
- Photolithography is a low-cost method that enables mass production and is typically accomplished with hot melt methodology. First, a cylindrical photoresist pattern is produced using photo-etching, and the top of the cylinder is melted into a smooth spherical surface. Ion-etching can then be used to transfer the colloidal shape to the substrate. The downside of this method is that surface tension control during the hot melt can limit the accuracy of the results.
- In femtosecond laser direct writing, an ultrafast laser is used to carve the desired structure, point by point, into a transparent material. This modern method enables a lens with any shape to be created without molds and makes it possible to produce stacked arrays or tilted lenses.
- Nano-imprint technology involves producing a metal template with the desired structure. The substrate is coated with a liquid polymer, and then stamped with the template. This is followed by ultraviolet curing and de-molding. Nano-imprint technology is a promising technique that can be used to mass produce aspheric and other complex surfaces, but the initial cost of manufacturing the metal template is very high.
- Micro injection molding again relies on a metal mold, but this one is prepared with micro-cavities for use with polymer arrays. A molten polymer is injected into the cavity, cooled, and then de-molded.
- 3D printing is another advanced method of microlens array production, in which photosensitive materials are stacked layer by layer. This method is capable of producing free-form surfaces and arrays of various shapes, but is currently not efficient.
Innovative Applications of Microlens Arrays
Microlens arrays have become an essential component of many optical systems. They are used for beam homogenization and shaping, for light collection, to focus light and increase efficiency. Emerging applications include:
- Autonomous driving: Microlens arrays are a key component of LIDAR, and can be used to dynamically control the laser emission angle to ensure both wide angle scans and high accuracy. A diffractive microlens array can also be integrated into car cameras, enabling a single sensor to capture IR and visible images simultaneously. This multispectral perception is key to safe driving at night and on foggy days. When microlens arrays are installed on a front windshield, they can focus projection information and dramatically improve the resolution of a head-up display.
- Imaging technology: Mobile camera imaging has been significantly improved by integrating microlens arrays into the sensor of a mobile phone camera to provide precise manipulation of incoming light. 3D face recognition, with face modeling down to the millimeter, depends on the thousand light points generated by microlens arrays. Another application is in endoscopy, where a microlens array can be mounted on a 2mm wide probe to provide high definition imaging.
- Laser processing: Microlens arrays are key to many advanced laser processing applications. In solar cell processing, photoelectric conversion efficiency depends on etching micron-scale conductive paths on the surface of the cell with a grid-like laser focus, provided by an array. The screens of full-screen mobile phones are precision cut by lasers guided by microlens arrays, and other arrays are used to increase accuracy and homogenize laser energy distribution for extreme ultraviolet chip lithography. (full-screen cutting, chip lithography, solar cell processing)
- Biomedical innovation: Labs-on a chip use microlens arrays to focus light on a micro spot and provide instantaneous detection of indicators like blood sugar and lipids. Microlens arrays are also used for Qualcomm gene detection and for implantable neuroimaging equipment in brain science research.
- Display and lighting: Many recent advances in display and lighting are directly related to the integration of microlens systems. Intelligent headlights for automobiles make use of programmable microlens arrays which are capable of adjusting beam shape dynamically as required by the environment. In cinema projection, microlens arrays can eliminate laser interference and the much-hated ‘snowflake noise’ of yesteryear. And in medicine, microlens arrays are used to collect light from a variety of sources to provide shadowless surgery lighting for safer procedures.
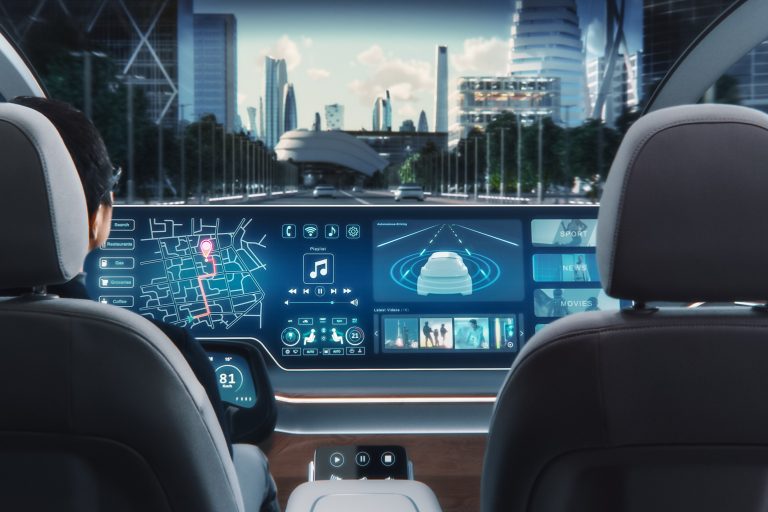
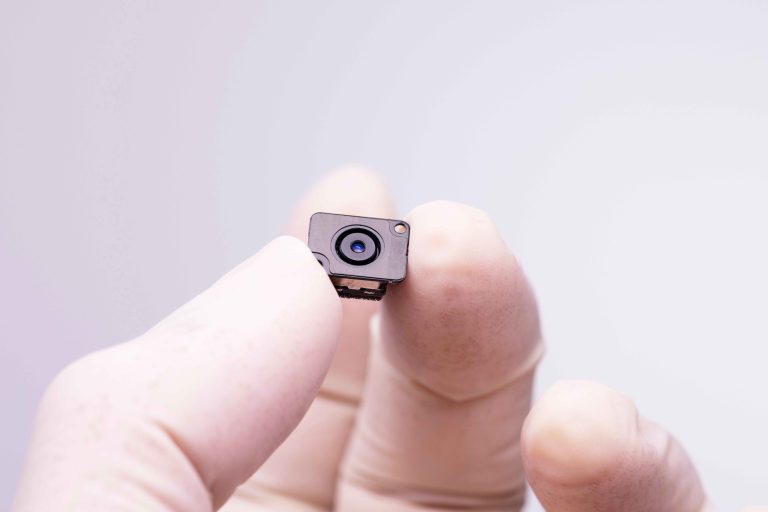
Custom Microlens Arrays
At Avantier, we specialize in creating custom optics that meet the exact needs of your application— and microlens arrays are one of our areas of expertise. Contact us today if you’d like more information or to set up an initial consult.
GREAT ARTICLE!
Share this article to gain insights from your connections!