Key Takeaways:
- Diamond like carbon coatings, along with other durable anti-reflective (AR) coatings, offer effective solutions for these systems.
- Optical systems operating in harsh environments face specific challenges related to preventing component damage and maintaining system performance.
- DLC coatings are known for their high hardness, low friction, and resistance to scratches and corrosion, while also providing excellent transmission in the mid- to long-wave infrared (IR) range.
- Their exceptional durability makes them well-suited for rugged environments, particularly in thermal imaging and defense applications.
What is DLC coating?
Diamond-Like Carbon (DLC) coatings are nanocomposite layers that mimic the properties of natural diamond, offering low friction, high hardness, and exceptional corrosion resistance. The structure and performance of DLC coatings depend on the ratio of SP3 (diamond) and SP2 (carbon) bonds, as well as the inclusion of elements like hydrogen, silicon, or metals.
DLC coatings are deposited using techniques like PVD arc, PVD sputtering, and PACVD processes, which can be tailored to produce hydrogenated or non-hydrogenated variants with specific performance characteristics. These coatings are environmentally friendly and help reduce friction, wear, fretting, galling, and corrosion. Additionally, DLC coatings can alter electrical conductivity and wettability.
DLC coatings play important roles specifically in optical components. They offer a perfect blend of aesthetics and performance across various industries, including automotive, aerospace, electronics, and medical devices.
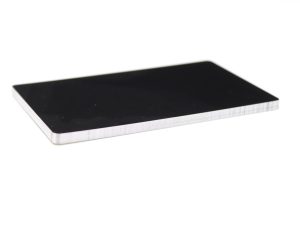
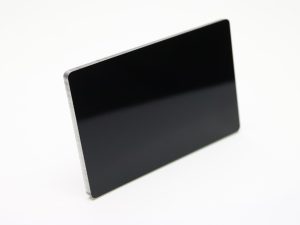
Core Benefits of Avantier’s Diamond-Like Carbon (DLC) Coatings:
- Exceptional Hardness and Wear Resistance: Avantier’s DLC coatings are incredibly hard, significantly improving the abrasion resistance of optical components. This prevents lenses and mirrors from deteriorating due to daily use, contact, and exposure to external environments, ensuring an extended lifespan and consistent performance.
- Ultra-Low Friction: The inherent lubricity of DLC coatings dramatically reduces friction between moving parts or against surfaces, which is critical in dynamic optical systems or those requiring precise mechanical interaction.
- Superior Chemical Inertness: Our DLC coatings are highly resistant to acids, alkalis, and other corrosive chemicals, ensuring stable performance even in aggressive operating environments.
- Proven Biocompatibility: For medical applications, DLC coatings are biocompatible, making them safe and effective for use on surgical instruments, endoscopes, and implantable devices.
Flawless Smooth Surface Finish: The application process results in an incredibly smooth surface finish, which minimizes light scattering and enhances overall optical clarity.
Type of DLC Coatings:
- Hydrogenated Amorphous Carbon (a-C:H): This type contains hydrogen and is typically used for applications where a combination of hardness and low friction is required.
- Tetrahedral Amorphous Carbon (ta-C): This type is nearly pure carbon and offers the highest hardness and durability, similar to natural diamond.

Roles of Diamond-Like carbon coatings in Optical Components
DLC coatings play several critical roles in optical components.
High durability
DLC coatings are extremely hard, and applying them to the surface of optical components improves abrasion resistance. This prevents lenses and mirrors from deteriorating due to daily use and exposure to external environments, ensuring a long lifespan.
Low reflectivity
DLC coatings significantly reduce surface reflection, which suppresses unwanted reflections and ghost images in optical systems, thereby enhancing optical performance. This is particularly important in applications requiring high-precision imaging.
Corrosion resistance and environmental resistance
DLC coatings are highly resistant to environmental factors such as acids, alkalis, and humidity. This allows optical components to maintain stable performance without corrosion or deterioration, even in harsh environments.
Wide wavelength range transparency
DLC coatings have excellent transparency across a wide range of wavelengths, from visible light to infrared. This makes them suitable for optical systems used across various wavelengths, with particularly strong effects in infrared optics.
Advanced Applications of Avantier’s Diamond-Like Carbon Coatings:
DLC coatings are widely used in fields demanding unparalleled durability and high optical performance.
- Military Optical Equipment: Providing crucial protection for thermal imaging systems, rangefinders, and surveillance optics used in challenging combat and reconnaissance environments.
- Precision Medical Instruments: Enhancing the longevity and performance of endoscopes, surgical lasers, and diagnostic tools, where reliability and biocompatibility are paramount.
- Industrial Laser Optics: Protecting high-power laser optics from damage in manufacturing and research settings, ensuring consistent beam quality and system uptime.
- Space Engineering & Exploration: Enabling long-term operation of satellite sensors, telescope components, and exploratory probes in the vacuum, extreme temperatures, and radiation of space.
- Ocean Exploration & Subsea Optics: Safeguarding underwater cameras, sonar systems, and deep-sea instruments from corrosion and abrasion in high-pressure, saline environments.
In these demanding applications, DLC coatings provide optical components with high durability and stability, significantly contributing to the overall performance and reliability of complex optical systems.
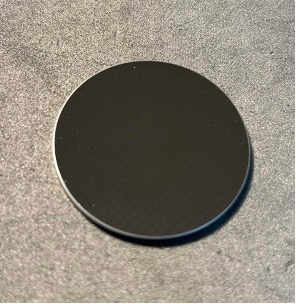
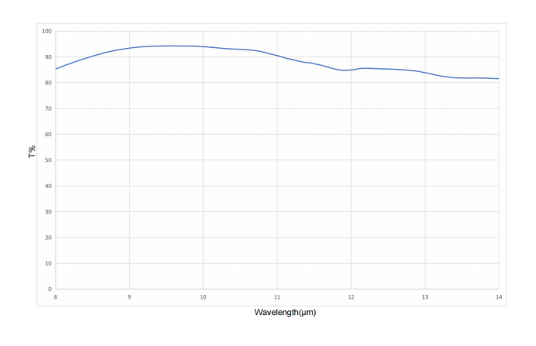
Diamond Like Carbon Coating Service from Avantier
Avantier specializes in the design and application of Diamond-Like Carbon (DLC) and other robust Anti-Reflective (AR) coatings. The preparation of DLC coatings leverages the unique properties of diamond and carbon atoms, including their specific bond angles and affinity with hydrogen atoms. This enables the creation of a structure analogous to natural diamond, forming a uniform, dense, and high-hardness coating on metallic substrates. This coating enhances mechanical strength, provides superior protection against wear and corrosion, improves tribological properties, and offers an enhanced aesthetic finish. We offer flexible engagement models: clients may either provide the substrate for the application of the DLC coating, or Avantier can fabricate the components according to specification and subsequently apply the DLC coating. Both options are available to meet our clients’ specific requirements.
Ready to enhance your optical components with our high-performance Diamond-Like Carbon coatings? Contact Avantier today for a consultation or quote.
GREAT ARTICLE!
Share this article to gain insights from your connections!