Key Takeaways
- Electromagnetic shielding grids (ESGs) in optical machining are essential for shielding sensitive equipment from electromagnetic interference (EMI).
- Customizable in aspects like shape, aspect ratio, and line width, these metal grids enhance shielding efficiency while maintaining high transmittance for optical needs.
- ESGs ensure signal integrity, measurement accuracy, and surface quality in high-precision settings.
- Widely used across aerospace, defense, and high-tech industries, ESGs enable precision machining in interference-free environments, adhering to strict electromagnetic compatibility (EMC) standards.
Electromagnetic Shielding Grids in Optical Machining
With rapid advances in electronics and wireless technology, electromagnetic interference (EMI) has become a major concern, often impacting the performance of sensitive equipment. ESGs have therefore become crucial, especially in optical machining, where electromagnetic stability is key. These fine metal meshes act as barriers against electromagnetic waves, creating a controlled environment that allows for high-accuracy operations. Here’s a closer look at how ESGs work, their core parameters, different types, and the roles they play in optical machining.
What is an Electromagnetic Shielding Grid?
An electromagnetic shielding grid is a metal mesh structure designed to reduce or block electromagnetic waves, EMI from affecting nearby devices. ESGs work by reflecting or absorbing the electromagnetic waves, creating a buffer zone around sensitive electronic or optical equipment. In optical machining—where accuracy is paramount—their use minimizes interference that could skew measurements, affect equipment stability, or impact machining quality.
- Grid Shape: ESGs are available in circular, random, or hexagonal configurations, with each shape offering unique shielding and transmission benefits. Circular grids, for example, may enhance transmission uniformity, while random grids suppress resonance at particular frequencies.
- Aspect Ratio: This is the ratio between the conductive material’s width and the grid’s total width. Higher aspect ratios boost shielding but may reduce transmittance, which is essential to balance in applications requiring both high shielding and optical clarity.
- Line Width and Width Ratio: In some ESGs, the width and spacing of grid lines are distributed randomly, which minimizes resonance with specific frequencies. Typically, line widths range from 0.1 mm to 1 mm, adjusted to accommodate specific application needs and frequency requirements. This versatility allows for tailoring the ESG to block out different interference frequencies effectively.
- Grid Spacing and Period: The spacing between grid lines significantly affects shielding at higher frequencies, with small grids commonly used in GHz applications for military and industrial purposes.
- Contact Resistance: Lower contact resistance (ideally below 1 milliohm) enhances the grid’s shielding performance by ensuring effective current transfer.
- Shielding Efficiency: Shielding efficiency measures the grid’s ability to block electromagnetic waves, typically expressed in decibels (dB). Higher efficiency (e.g., -60 dB to -100 dB) is necessary in military or high-tech industrial settings, where EMI could jeopardize sensitive operations. For example, an efficiency of -80 dB in a 1MHz to 1GHz range can significantly reduce interference, creating a controlled environment essential in optical machining.
- Transmittance: In optical applications, ESGs must often balance transparency and shielding. Optical transmission grids can achieve transmittance as high as 80-90% for visible applications. For infrared or other wavelength-specific uses, transmittance can be adapted between 50% and 85%, ensuring that the shielding properties do not impede optical performance.
Types of Electromagnetic Shielding Grids
Different grid types are chosen based on specific requirements:- Metallic Grids: Made from copper, tin, or stainless steel, they provide excellent conductivity and durability, common in aerospace and petrochemical applications.
- Ferromagnetic Grids: Built from materials like permalloy, these grids are effective for shielding low-frequency magnetic fields.
- Composite Grids: Combining materials such as copper and permalloy, they offer broad shielding across multiple frequency ranges.
- Advanced Materials (e.g., Graphene Grids): Graphene’s lightweight, transparent, and low-reflective properties make it ideal for high-tech applications that demand both shielding and optical clarity.
Applications of Electromagnetic Shielding Grids in Optical Machining
ESGs play a vital role in maintaining precision and stability in optical machining:
- Protecting Sensitive Components: High-precision optical machining equipment integrates sensitive electronic components, including sensors, controllers, and lasers. These parts are highly susceptible to EMI, which can disrupt performance or even damage delicate circuitry. ESGs shield these components, ensuring accuracy and durability over prolonged use.
- Improving Measurement Accuracy: Measurement accuracy is essential in optical machining, where even minor inaccuracies can lead to substantial defects. EMI can impact instruments like lasers and beam modulators, causing data deviations. ESGs help maintain measurement precision by reducing EMI, resulting in consistently accurate data.
- Ensuring Signal Integrity: During optical machining, signal integrity is vital for transmitting accurate data. ESGs placed strategically within the equipment prevent EMI from distorting signal clarity, which directly impacts machining precision and effectiveness.
- Maintaining Surface Quality of Workpieces: In certain processes, EMI can introduce vibrations or temperature fluctuations that affect the workpiece’s surface finish. By stabilizing the environment, ESGs reduce the chances of surface imperfections, leading to higher-quality machining outcomes.
- Meeting Electromagnetic Compatibility (EMC) Standards: ESGs help ensure compliance with stringent EMC standards, aiding certification and market readiness.
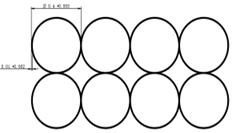
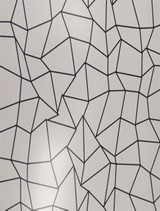
Customization and Design Options
The versatility of ESGs allows them to be customized to various shapes—such as random, circular, or hexagonal—suitable for curved surfaces, spherical windows, or other non-standard designs. Avantier’s ESGs are tailored to meet the exact needs of aerospace, defense, and precision machinery sectors, ensuring robust shielding without compromising flexibility.
Conclusion
Electromagnetic shielding grids have become integral in optical machining, providing EMI protection while preserving accuracy and quality. By selecting and customizing ESGs based on grid shape, line width, and shielding efficiency, Avantier enhances reliability, measurement accuracy, and surface quality. These advanced shielding solutions ensure that precision optical machining can occur in stable, interference-free environments, meeting industry standards and enabling the production of high-quality components.
GREAT ARTICLE!
Share this article to gain insights from your connections!