Key Takeaways
- Laser Metrology uses laser interferometers with specific wavelengths and semi-reflectors for precise measurements.
- It is crucial in fields like medical device manufacturing, aerospace, automotive engineering, and semiconductor fabrication.
- Techniques include optical frequency metrology, scanning laser vibrometry, and holographic interferometry using semi-reflectors.
- Environmental factors like temperature and humidity affect measurements, with applications like LIGO observing gravitational waves.
Applications of Laser Metrology in Industry and Research
Laser metrology involves the use of lasers to take measurements and test equipment. A versatile set of techniques that enables quick, highly precise, contact-free measurements, laser metrology has an important place in process oversight and quality control. Fields that rely on laser metrology include:
- Medical device manufacturing
- Aerospace quality control
- Automotive engineering
- Semiconductor fabrication
Laser metrology is also used in scientific research, for instance, in the exploration of nanoscale structures or the elucidation of quantum phenomena.
Forms of Laser Metrology
But just how does laser metrology work, and in what form it is most successfully used for these applications? Laser metrology has many different forms. Optical frequency metrology with frequency comb lasers is used in physics research to precisely measure the properties of calculable atoms and molecules.
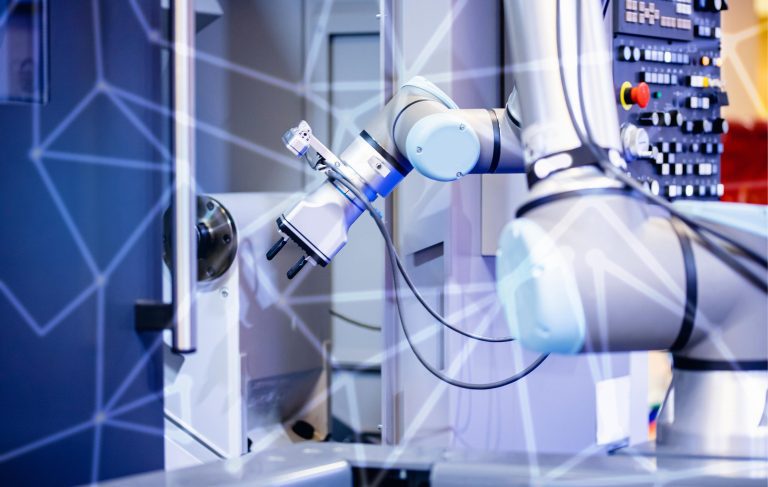
Scanning laser vibrometry can be used to determine the vibration velocity distribution at specific points of an object such as an engine, and enables automobile engineers to analyze the structure-born noise of a car body and optimize its interior acoustical behavior. Holographic interferometers illuminate the vibrational behavior of the components of brakes and elucidate their behavior during braking. Hand-held laser trackers are used to measure distances and smoothness of aerospace parts.
In this article we’ll take a look at a basic laser interferometry setup. A laser interferometer is a device that uses laser interference patterns to measure distances between objects, inspect parts for straightness, parallelism, and flatness, and calibrate slip gauges and machine tables. It can provide precision measurements accurate to less than a nanometer, and its noncontact nature makes it ideal for measuring objects that are fragile or delicate.
The Design and Function of a Laser Interferometer
A laser interferometer consists of a fixed unit and a moving unit, and (connected to the fixed unit), an amplifier and a digital counter. The fixed unit houses the laser source, two photodiodes, and two semi-reflectors. The type of laser head used will vary depending on the application; some possibilities include He-Ne lasers, He-Cd lasers, solid state lasers, or diode lasers.
Within the fixed unit, the photodiodes measure fringe intensity and displacement. A corner cube is mounted on the moving unit; a glass disk with three polished faces at right angles to each other. This corner cube reflects any light at an angle of 180.
The image below shows a schematic diagram of this setup, a variant of the Michelson interferometer.
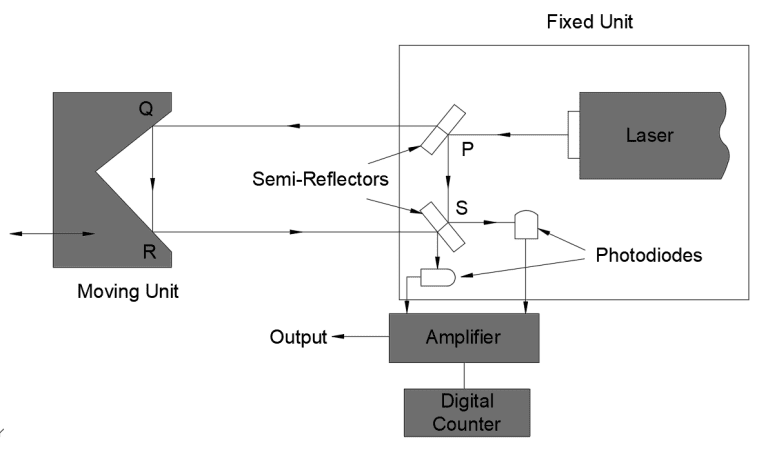
When a laser interferometer is used, the laser beam travels from the light source to the first semi-reflector (labeled P above) where it is split into two beams. A portion of the light is reflected by ninety degrees and this incoming beam hits the second reflector (labeled P). Another portion of the light passes through P, hits the corner cube, is turned around 180 and sent back to the semi-reflector S.
Destructive interference will occur if the distance between the two beam paths is an odd number of half wavelengths; in this case, a minimum diode output is obtained. Where the difference is an even number of half wavelengths, constructive interference means the photodiode will give a maximum output.
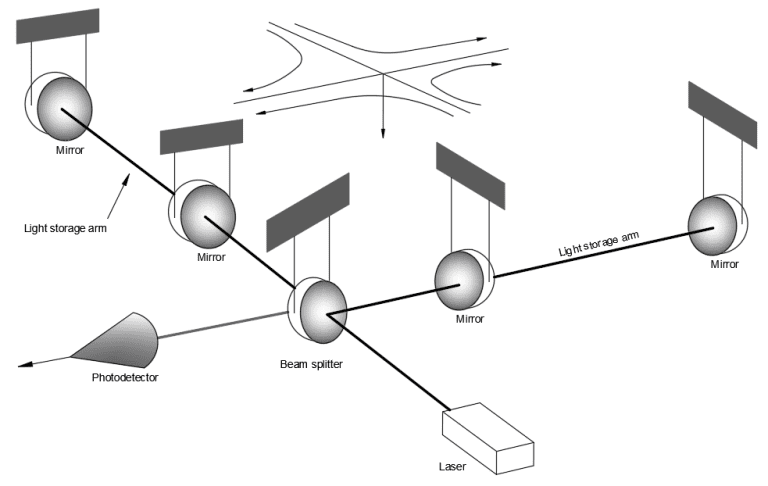
As the moving slide is displaced, the output will change from maximum to minimum over every half wavelength, producing sinusoidal output. This output is then processed by the amplifier and high-speed counter to produce a displacement reading, in millimeters or microns.
For instance, if you were using a laser beam at wavelength 633 nm, the detector would note a change from light to dark each time the moving piece is moved by 316.5 nm. In a general case, the displacement can be calculated as (wavelength of laser)(number of fringes passed)/2 .
It is important to note that the distance calculations are entirely dependent on the wavelength of the laser, and in practice, this will depend on the refractive index of the air in the operating environment. Changes in air temperature, air pressure, and relative humidity will affect the laser wavelength, and this must be taken into account.
One interesting application of a laser interferometer involves measuring gravitational waves, which may cause movements of as little as 1/10,000th of the length of a proton. An example of this is Caltech’s LIGO laser interferometer gravitational wave observatory, which measures gravitational waves with an interferometer built on the same pattern as Michelson’s, but with arms km long. This interferometer has been used to measure such things as black hole mergers and colliding neutron stars.
GREAT ARTICLE!
Share this article to gain insights from your connections!