Key Takeaways
- Optical coatings encompass a range of technologies, including reflective and dielectric coatings, enhancing optical components’ performance.
- Alexander Smakula pioneered optical coatings in 1935, starting with single-layer anti-reflection coatings.
- Key coating technologies today include Ion Beam Sputtering and Plasma-Assisted Reactive Magnetron Sputtering, each offering specific benefits for optical applications.
An optical coating is a vital technique with many applications, including creating glasses for those with light-sensitive eyes and improving camera lenses. This article will cover all you need to know about optical coatings, such as what it is, how it works, and various types and technology.
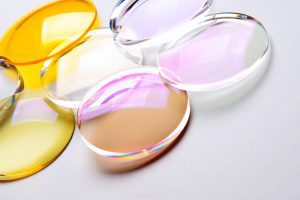
What Is Optical Coating?
What is the optical coating? An optical coating is a layer of a very thin film that is applied to the surface of an optical component to improve transmission, modify reflecting qualities or alter the polarization of the light emitted by the component.
A coating can be as basic as a sheet of metal, such as aluminum, or it can be as complex as a dielectric coating made of several thin layers of material, with precisely regulated parameters for the thickness, composition, and number of layers.
Coatings have been actively contributing to the optical industry since the year 1935. Both the innovation and the initial method, which involved using a single layer of anti-reflection coat, were patented by Alexander Smakula. Since the company’s inception, Smakula has relied on vacuum technology to incorporate a fluoride component into glass lenses. However, this results in undesirable reflection.
Since then, new production techniques have been established, and the coating operations for optical components have been refined and altered to become more productive and affordable.
Types of Optical Coatings
Several types of optical coatings function differently to produce results based on use. Here are some of those types.
- Filter Coatings: These optical coatings can improve or degrade the appearance of an image by applying one or more thin layers to a substrate. Optical filter coating can also reflect specific wavelengths during picture transmission.
- Beam Splitter Coatings: A beam splitter coating can divide a single light beam into two separate beams, typically with a transmission-to-reflectance ratio being equal or varying value. Depending on the use case, they can also manage multiple beam pathways, recombine those routes, and control the polarization of the combined beams.
- High-Reflective Coating: The surface to which a high-reflective coating is placed reflects all or part of the light that strikes it. For instance, a glass optic that has not been coated would have a reflection of 4%. Metal coatings, on the other hand, will fundamentally change the features of the optic. For example, using an aluminum coating on the same optic will cause it to reflect around 88-92% of visible light. Silver coatings, when used in conjunction with the appropriate dielectric coating, have the potential to increase reflectivity in the far infrared band to 99.9%. (reflection will be less in the UV and some visible spectrum regions). Dielectric mirrors often have coatings consisting of two distinct repeating layers: one layer with a high index (such as TiO2 or ZnS) and one with a low index. These two levels are typically separated by an intermediate layer (e.g., MgF or SiO2). These highly reflective dielectric coatings have a reflectance that is exceedingly high over the band stop, which is a relatively narrow range of wavelengths. To put it more concisely, HR coatings are essential for the proper operation of laser equipment since they reduce the amount of laser power required for various applications.
- Anti-Reflective Coating: It is common practice to apply an anti-reflection coating (also known as an antiglare coating) to the surfaces of lenses and other optical elements in order to cut down on reflection. When there is less reflection, the results of image capture are significantly enhanced. Tools such as cameras, binoculars, telescopes, and microscopes can all benefit from having anti-reflective coatings applied to their surfaces. This is because the elimination of stray light improves visual contrast, resulting in a decreased amount of light reflection. Opticians can apply the anti-reflective coating to the lenses of eyeglasses to ensure that people around them can see the person wearing the glasses. In addition, the antiglare coating can successfully reduce glint from binoculars or telescopic lights that clandestine observers utilize.
Coating Technologies
Optical coatings are suitable for use with various well-known processes, including physical vapor deposition. Each of them possesses unique benefits that place it in a position to be the most suitable alternative for a given set of use cases, some of which overlap. However, none of them is best suited for all applications. The following are the optical coating technologies that are most commonly used.
- Ion-Assisted Electron-Bean (IAD E-Beam) Evaporative Deposition Electron-Bean Assisted Ionization (IAD E-Beam) Evaporative Deposition is a technique that involves bombarding and vaporizing source materials in a vacuum chamber with an electron gun. This technique provides the most coating design flexibility of any other method on this list. This is due to the fact that it is capable of utilizing the greatest variety of materials, is the least expensive of all the processes, and is able to combine substantially larger coating chamber sizes. Therefore, this is the most effective technique when one is more concerned with low cost and great flexibility than with good performance.
- Ion Beam Sputtering (IBS) :Coatings created using Ion Beam Sputtering (IBS) are of exceptional optical quality and stability, and the process is very repeatable. The ability of IBS to accurately monitor and manage elements such as oxidation level, layer development rate, and energy input is a significant benefit that enables extremely reproducible coatings to be generated. This capacity allows for IBS to be used to produce exceptionally durable coatings. IBS is more resistant to the impacts of temperature and humidity than other technologies are when compared with those technologies. However, it does have a few negatives to consider. IBS coatings have a significantly higher relative cost when compared to the other techniques. They also have slower growth rates, smaller chamber sizes, and more UV spectrum stress and loss.
- Plasma-Assisted Reactive Magnetron Sputtering (PARMS) :During the process of PARMS, a glow discharge plasma is used to accelerate positive ions onto the target. This plasma is restricted by a magnetic field to an area surrounding the target. This causes atoms to be ejected, which then causes them to spread out and cover the optical surface. Because this procedure can function smoothly even with a low chamber pressure, there is no need for any setup to be done before beginning it. PARMS does not have quite the same level of repetition as IBS, but it does have a high throughput, and it is significantly more repeated than evaporative deposition. In addition to this, the coatings of the films are typically tough and dense. Because of its perfect equilibrium between its optical performance and volume throughput, it is ideally suited for application as a fluorescent optical filter.
- Advanced Plasma Sputtering (APS) :Advanced Plasma Sputtering (APS) refers to a method of evaporative deposition that uses the same principle as IAD E-Beam but benefits from more sophisticated forms of automation in the processing stage. When using APS, we get smooth, dense, and hard coatings, and they provide more consistent optical qualities than IAD E-Beam. For several characteristics that vary between IBS and IAD E-Beam evaporative deposition, APS and magnetron sputtering can be regarded as intermediate solutions.
Conclusion
As a result of developments in technology, there has been an increase in the market for optical coatings. This is because there has been a rise in the consumption of electronic goods and semiconductors. With various applications and benefits, from use in glasses to use in lenses, the optical coating is a technology that should not be overlooked. Please contact us if you’d like to schedule a consultation or request for a quote on your next project.
GREAT ARTICLE!
Share this article to gain insights from your connections!