Key Takeaways:
- Super High Durability optical coatings (SHD Optical Coatings) enhance IR window performance with high transmission efficiency, scratch and chemical resistance, anti-reflective properties, and environmental resilience.
- Designed for aerospace, military, and industrial applications, SHD coatings maintain signal clarity in harsh environments, resist abrasion and chemical exposure, and withstand temperature fluctuations.
- Compared to conventional coatings, SHD coatings extend the lifespan and reliability of IR systems, making them essential for demanding operational conditions in high-stakes fields.
In the realm of optical technology, where precision, durability, and high performance are paramount, Super High Durability (SHD) coatings stand out as essential advancements. SHD coatings are engineered specifically for infrared (IR) windows, meeting the need for enhanced durability, efficient transmission, and strong environmental resistance. They find widespread use in aerospace, military, and industrial applications, where IR systems endure harsh conditions. This article explores the critical features of SHD coatings, highlighting their significance and benefits over conventional coatings.
Key Characteristics of Super High Durability Coatings
SHD optical coatings possess distinct properties that enable high performance under challenging conditions. Here are their core characteristics and technical composition:
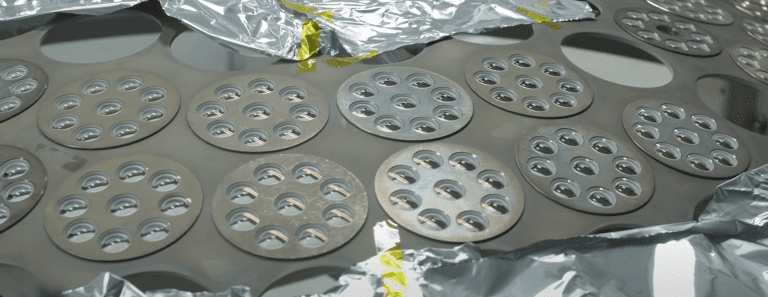
1. High Transmission Efficiency
Efficient IR transmission is crucial for systems like infrared windows, and IR-guided equipment, where clarity and signal strength are crucial.
– Material Composition: SHD coatings use materials with high transparency within IR wavelengths, particularly in the mid-wave infrared (MWIR) range of 3–5 μm and the long-wave infrared (LWIR) range of 8–12 μm. Materials such as zinc sulfide (ZnS), zinc selenide (ZnSe), and IR-compatible glasses are common in SHD coatings due to their favorable transmittance properties.
– Layer Optimization: Constructed with multiple layers optimized to minimize reflection by matching refractive indices between the coating, substrate, and environment, these coatings reduce light loss and ensure minimal interference.
– Application Significance: High transmission efficiency is indispensable in applications where signal quality is vital, such as thermal sensors, IR spectroscopy, and military-grade targeting systems.
2. Durability
SHD coatings withstand abrasive and chemically aggressive environments, making them ideal for industrial, aerospace, and defense applications.
– Abrasion and Scratch Resistance: By incorporating ultra-hard materials like diamond-like carbon (DLC), SHD coatings provide a robust, scratch-resistant surface suitable for abrasive environments.
– Chemical Resistance: Equipped with chemical-resistant layers, SHD coatings shield IR windows from substances like acids, alkalis, and solvents—critical in industrial and military settings where exposure to fuels and cleaning agents is common.
– Adhesion Strength: Techniques like ion beam-assisted deposition (IBAD) and plasma-enhanced chemical vapor deposition (PECVD) enhance adhesion, creating a stable, durable finish that extends the lifespan of IR systems.
3. Anti-Reflective Properties
Reducing surface reflection is essential in infrared optics, where even minor losses can disrupt imaging.
– Reflection Minimization: SHD coatings incorporate multi-layer anti-reflective (AR) structures that alternate between high- and low-refractive-index materials. These layers work synergistically to counteract reflection losses, ensuring more IR light passes through the window with minimal reflection.
– Enhanced Imaging: By lowering surface reflections, SHD coatings improve the signal-to-noise ratio in IR systems, resulting in clearer and more accurate imaging. This enhancement is especially beneficial in thermal sensors, where precise imaging quality is essential for effective target detection and monitoring.
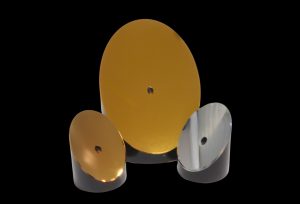
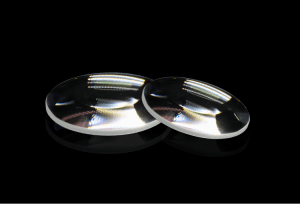
4. Environmental Resistance
SHD coatings provide strong resistance to temperature fluctuations, humidity, water, and particulate exposure, making them suitable for extreme environments.
– Temperature Resistance: Tolerating temperatures up to 300–500°C, depending on the substrate, SHD coatings are suitable for aerospace and high-temperature applications where thermal stability is critical.
– Humidity and Water Resistance: Treated with hydrophobic and oleophobic layers, SHD coatings repel water and resist humidity, maintaining clarity in moist environments, which is valuable in outdoor surveillance or meteorological applications.
– Dust and Debris Resistance: Certain SHD coatings incorporate anti-static layers that repel dust, which is particularly beneficial in environments like manufacturing plants, where airborne particles are prevalent. This feature minimizes the need for frequent cleaning, maintaining clear optical pathways and extending the service life of IR windows.
Technological Applications and Market Significance
SHD coatings provide benefits across multiple industries:
– Aerospace and Defense: In military-grade systems like missile guidance, thermal imaging, and target acquisition, SHD coatings deliver consistent performance and reliability, enhancing mission success rates and equipment longevity.
– Industrial Monitoring and Environmental Control: Industrial applications rely on SHD-coated IR windows for high-temperature monitoring and emissions control in harsh environments, where resilience to abrasion and chemicals is critical.
– Medical and Scientific Research: In medical and scientific fields, SHD coatings support accurate IR spectroscopy and thermal imaging by maximizing transmission and minimizing interference from environmental factors. These qualities are essential in applications like non-invasive diagnostics and detailed spectroscopic analysis.
Comparing SHD Coatings with Conventional Coatings
While conventional coatings are effective in standard conditions, they may lack the durability required in harsh IR applications. Standard anti-reflective coatings may degrade under high abrasion or chemical exposure. SHD coatings, by contrast, are tailored for infrared wavelengths and constructed to withstand physical and environmental stresses, offering superior transmittance, durability, and environmental resistance, ultimately enhancing IR systems’ service life and performance.
Conclusion
SHD optical coatings represent a sophisticated solution for infrared windows, enabling durability and resilience in demanding environments. With high transmission efficiency, scratch and chemical resistance, anti-reflective capabilities, and environmental stability, SHD coatings play a critical role in defense, aerospace, and industrial applications. As industries demand greater reliability from IR systems, SHD coatings offer a transformational enhancement that ensures longevity and quality in the most challenging optical applications.
In essence, SHD coatings are more than an addition to IR windows—they are a vital advancement, ensuring consistent performance and reliability for today’s high-stakes optical technologies.
GREAT ARTICLE!
Share this article to gain insights from your connections!