Key Takeaways
- Avantier specializes in high-precision microscope objectives.
- Our process involves detailed optical and mechanical design, precise lens fabrication, meticulous structural part machining, careful lens group assembly and debugging, rigorous installation and adjustment, and final re-inspection and secure packaging.
- Our state of the art design and manufacturing processes ensure high-performance objectives for diverse applications.
Introduction to Manufacturing High Resolution Microscope Objectives
With over two decades of experience in optical engineering and manufacturing, our company specializes in the design and production of high-precision microscope objectives. Our portfolio encompasses a wide range of standard and specialized objectives, from conventional 2X to 100X flat field designs to advanced supercomplex metachromatic objectives. This article provides a detailed technical overview of our manufacturing process, focusing on the production of a 20X microscope objective as a representative example.
- Optical Design
The process of designing a new objective begins with meticulous optical design, driven by customer specifications and application requirements.
- Requirement Analysis: Optical engineers analyze customer-defined parameters, including usage requirements, lens specifications, and acceptance criteria.
- Design and Simulation: Utilizing advanced optical design software (e.g., ZEMAX), engineers develop and optimize the optical system.
Tolerance Analysis: Critical to manufacturability, engineers refine tolerances for optical components, ensuring ideal performance within production capabilities.
Engineering Drawings: Aided by state of the art design software, the team generates detailed engineering drawings for all optical elements.
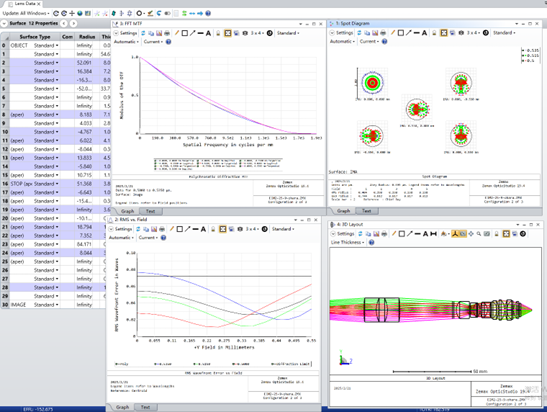
- Architectural Design
- Mechanical Requirements: Structural design factors in all customer-specified mechanical parameters, including external dimensions and interface threads.
- Manufacturing Constraints: Engineers optimize structural tolerances, surface treatments, and material selection based on production processes.
- Engineering Drawings: Comprehensive engineering drawings for all structural components are created.
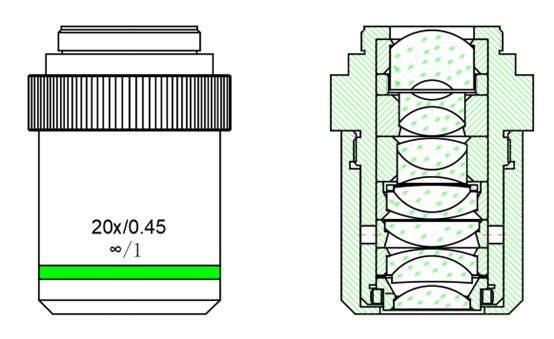
- Lens Processing
- Process Planning: Process engineers generate detailed process diagrams, including lens drawings, tooling requirements, and manufacturing sequences.
- Material Preparation: Raw optical materials are cut to precise dimensions according to process drawings.
- Grinding:
- Coarse Grinding: Initial shaping of the lens blank is done using coarse grinding methods.
- Fine Grinding: Precise shaping of the lens radius (R value) and thickness is accomplished by fine grinding that may be computer-guided.
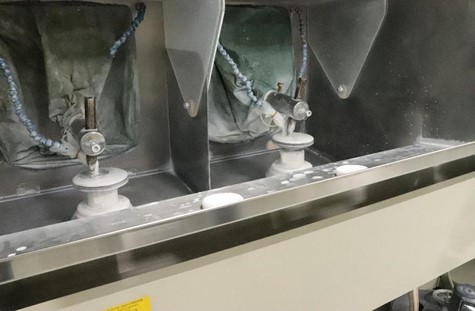
- Polishing: After the lens is shaped, the required surface finish is achieved through various polishing techniques (classical, low throw, high throw).
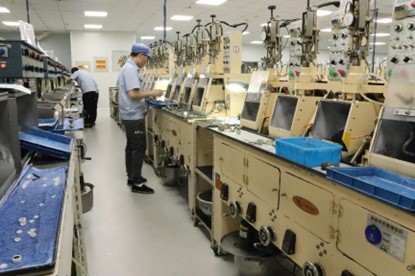
- Edging: The outer diameter of the newly polished lens is then ground to specified dimensions.
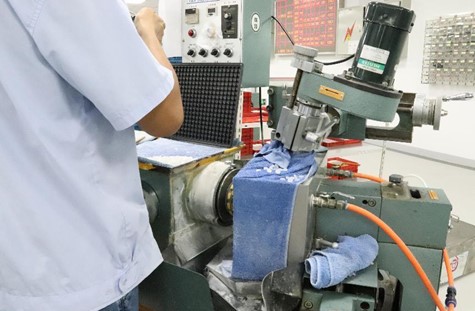
- Inspection: After the edging is finished, rigorous testing using interferometers, projectors, micrometers, and calipers is done to verify lens dimensions and surface quality.

- Cleaning: Ultrasonic cleaning is used to remove contaminants, and this cleaning is followed by cleanliness inspection.
- Coating: For many lenses, the next step in the process is the application of optical coatings using vacuum deposition techniques to meet spectral requirements.
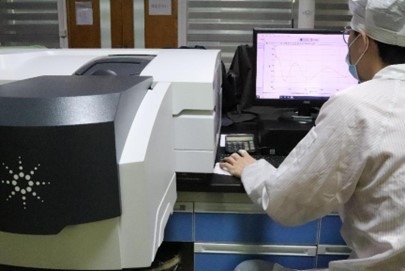
- Cementing: Bonding multiple lens elements is accomplished using UV-curable adhesives, with precise centering adjustments.
- Blackening: Application of black ink to lens edges is done to minimize stray light.
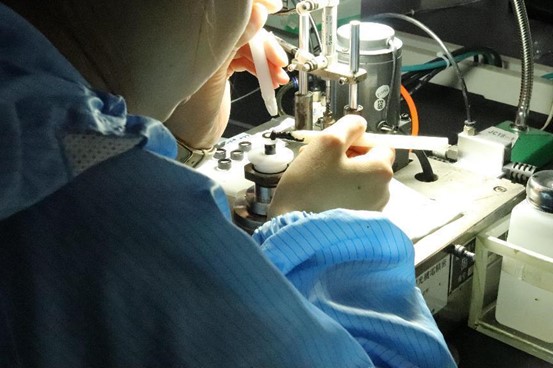
- Final Inspection and Storage: When the edging is complete, we run a comprehensive inspection of lens parameters and surface cleanliness, followed by packaging and storage in a controlled environment.
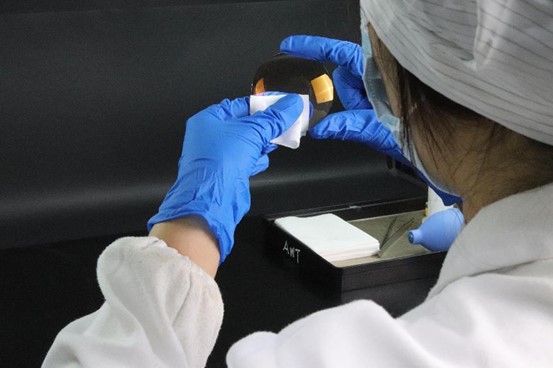
- Structural Parts Processing
- Process Planning: Process engineers develop detailed process drawings and tooling requirements.
- Material Preparation: Raw materials are cut to specified dimensions.
- Machining: Precision machining is done with lathes, milling machines, and other equipment.

- Inspection: All parts are subject to dimensional and geometric verification using coordinate measuring machines (CMMs) and other metrology equipment.
- Surface Treatment: After inspection, surface treatments such as anodizing, sandblasting, and electroplating are done as required.
- Final Inspection and Storage: Comprehensive inspection and packaging is done in a controlled environment.
- Mirror Group Assembly and Debugging:
- Assembly Techniques: Two important techniques are employed in assembly: point glue repair and optical axis turning.
- Point Glue Repair: Point glue repair involves precision alignment and bonding using UV-curable adhesives.
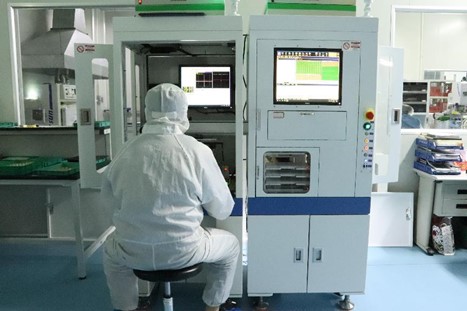
- Optical Axis Turning: Precision machining is done to ensure concentricity and perpendicularity of lens elements.
- Lens Installation and Adjustment:
- Objective Debugging: Assembly and adjustment of the objective lens is accomplished using a microscope frame and star target observation.
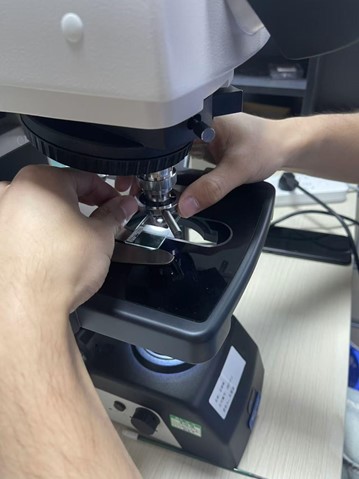
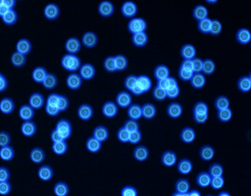
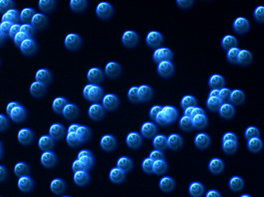
- Resolution Testing: A resolution target is used to evaluate and test the objective resolution.
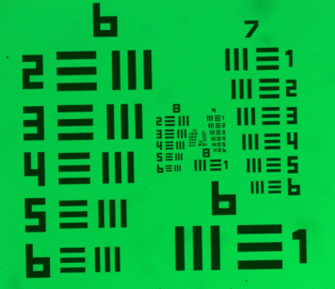
- Focal Length Adjustment: The objective lens focal length is adjusted through precision machining.
- Re-inspection and Packaging:
- Re-inspection: Comprehensive testing of assembled objectives is done using star target observation and MTF testing.
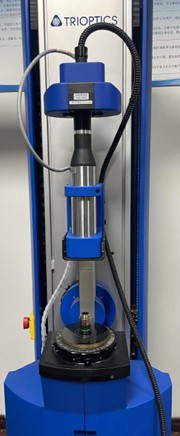
- Packaging: The objective is securely packed to ensure comprehensive protection during shipping and storage.
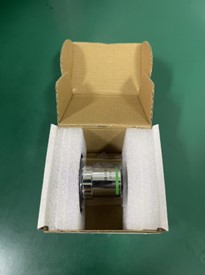

Manufacturing High Resolution Microscope Objectives
The manufacturing of high precision microscope objectives is a complex and demanding process requiring expertise in optical design, precision machining, and assembly. Our company’s commitment to quality and continuous improvement ensures the delivery of high-performance objectives for a wide range of applications.
Related Content
GREAT ARTICLE!
Share this article to gain insights from your connections!