Key Takeaways
- Role in Optical Manufacturing: Optical polishing ensures high surface accuracy, low roughness, and minimal damage, leading to superior light behavior.
- Precision Polishing Methods: Techniques such as CCOS, IBF, MRF, Reactive Plasma Polishing, and Precision Diamond Cutting address advanced precision demands.
- Applications: Precision polishing techniques support diverse geometries, hard materials, and high-performance systems, including telescopes and lithography tools.
- Challenges: High costs, technical expertise, and inefficiencies in large-scale polishing remain significant obstacles.
- Future Impact: Advancements in optical polishing will drive innovation and elevate optical manufacturing performance.
Modern Optical Polishing Techniques
Precision optical components form the cornerstone of modern optical systems, playing a pivotal role in determining the performance and quality of optical devices. Transforming optical raw materials into functional components involves several steps: blank forming, rough grinding, fine grinding, polishing, and coating. High quality optical components exhibit high surface accuracy, low surface roughness, and minimal surface damage. These characteristics directly influence light behavior—high surface accuracy minimizes deviation, and low roughness reduces light scattering.
Among the critical stages in optical manufacturing, polishing is fundamental to achieving the desired processing precision and product performance.
The Purpose and Evolution of Optical Polishing
Optical polishing removes surface imperfections like small bumps and scratches, rendering the material smooth and mirror-like. The polishing process impacts surface shape accuracy, roughness, finish, and transparency. Traditional polishing methods rely on mechanical friction and chemical erosion. However, the increasing complexity and precision requirements of modern optical systems—particularly for aspherical and freeform surfaces—demand advanced lens polishing techniques.
Advanced precision machining technologies enable sub-nanometer or even nanometer-level accuracy, making them indispensable for high-performance optical systems. These techniques ensure stable, precise machining for specialized components, elevating modern optical lens polishing to a highly sophisticated process.
Precision Polishing Methods
1. Computer-Controlled Optical Surfacing (CCOS)
Computer-Controlled Optical Surfacing (CCOS) uses numerically controlled polishing tools to achieve high precision. This modern contact polishing technique relies on computer algorithms to model the surface and guide the movement, speed, pressure, and dwell time of polishing heads. By incrementally removing material, CCOS reduces errors and achieves the desired surface accuracy.
CCOS has been instrumental in fabricating high-precision components such as the Hubble Telescope’s primary mirror and the Extremely Large Telescope (ELT).
Advantages | Limitations |
Suitable for diverse geometries, including aspherical and freeform surfaces. | Low efficiency for polishing large-diameter components due to small tool heads. |
Allows localized adjustments for regional errors. | Requires skilled programming and operation |
Widely used for producing components like aspherical lenses. |
2. Ion Beam Figuring (IBF)
Ion Beam Figuring is a non-contact polishing method where an ion beam removes material at an atomic level. The interaction between ions and material atoms ensures precise shape correction and surface refinement.
IBF is particularly useful in aerospace optics, where lightweight and rigid components are crucial.
Advantages | Limitations |
High precision with minimal surface damage or internal stress. | Low material removal rate. |
Effective for hard materials like silicon (Si) and silicon carbide (SiC). | |
Ideal for applications requiring atomically smooth and polished surfaces, such as extreme ultraviolet lithography systems. |
3. Magnetorheological Finishing (MRF)
Magnetorheological Finishing uses a fluid with variable viscosity under a magnetic field. This fluid, containing abrasive particles, forms a controlled polishing interface for micro- and nano-level material removal.
MRF is widely used for polishing spherical lenses, aspherical lenses, prisms, and freeform surfaces.
Advantages | Limitations |
High precision with no subsurface damage. | High equipment and maintenance costs. |
Suitable for complex geometries, such as freeform surfaces. | Inefficient for large-scale rough polishing. |
Adjustable hardness of the polishing interface. |
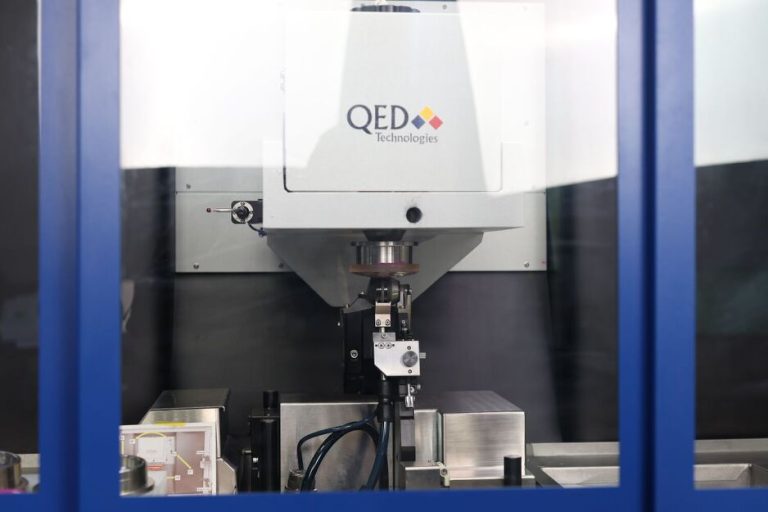
4. Reactive Plasma Polishing
Reactive Plasma Polishing employs chemical etching in a vacuum chamber to achieve ultra-smooth surfaces. Plasma and reactive gases remove material at the atomic level, making this a non-contact polishing method.
This technique is often used for the final finishing of high-precision components.
Advantages | Limitations |
High material removal efficiency with sub-nanometer surface roughness. | High equipment costs and technical expertise requirements. |
Ideal for large-aperture, high-hardness, and brittle materials.Pollution-free and damage-free |
5. Precision Diamond Cutting
Precision Diamond Cutting uses ultra-precision lathes and diamond tools to directly cut optical surfaces. Diamond’s hardness and thermal resistance ensure smooth, mirror-like optical finishes.
Common uses include laser mirrors, parabolic mirrors, and infrared lenses.
Advantages | Limitations |
Rapid processing with sub-micron accuracy. | Potential for microscopic scratches, requiring post-processing for higher quality finishes. |
High-quality surfaces suitable for immediate use in some cases. | Limited suitability for specific surface geometries. |
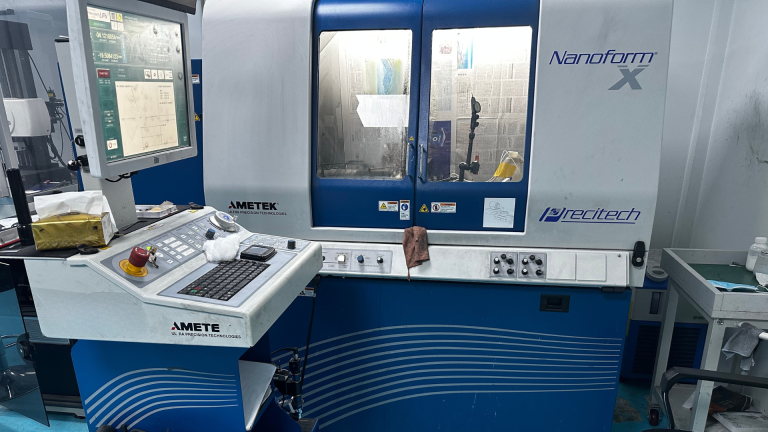
Precision Optical Polishing Techniques
Modern optical polishing techniques have revolutionized the manufacturing of optical components, meeting the stringent demands of advanced optical systems. From CCOS to Reactive Plasma Polishing, each method offers unique advantages tailored to specific optical materials and applications. As technology advances, these techniques will play an increasingly critical role in pushing the boundaries of optical performance.
GREAT ARTICLE!
Share this article to gain insights from your connections!