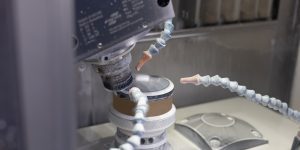
WE CAN HELP YOU!
Contact us NOW for sales & expert advice.
Spherical Aberration Correction
One of the most important features of aspheric lenses (ASP Lens) is their ability to correct for spherical aberration. Spherical aberration is found in all spherical lenses, such as plano-convex or double-convex lens shapes. However, aspheric lenses excel in focusing light to a precise point, resulting in minimal blur and enhanced image quality. Spherical Aberration is the consequence of the uniform curvature of the lens surface and not the result of a manufacturing error. The outer rays converge at a different focal point than the inner rays resulting in blurred or distorted images.
A spherical lens with a significant amount of aberration and an aspherical lens with almost no aberration can be seen(Figure 1). Aspherical Lenses address the issue by deviating from a perfectly spherical shape. An aspheric lens can be designed by modifying the curvature length and adjusting the conic constant and aspheric coefficients of the curved surface of the lens. By carefully shaping the lens, aspheric lenses ensure that all incoming light rays converge to a single focal point. minimizing spherical aberration and improving image quality.
In Figure 1, the difference in focusing performance of spherical lenses and aspheric lenses is further explained by the table below. It compares the performance of a spheric lens and an ASP Lens both with a diameter of 25mm and focal lengths of 25mm (f/1 lenses). The table presents a comparison of spot sizes, or blur sizes, for collimated 587.6nm light rays under different conditions: on-axis (0° object angle) and off-axis (at 0.5° and 1.0° object angles). The spot sizes of the asphere are significantly smaller, differing by several orders of magnitude compared to those of a spherical lens.
Object Angle (°) | 0.0 | 0.5 | 1.0 |
Spherical Spot Size (μm) | 710.01 | 710.96 | 713.84 |
Aspheric Spot Size (μm) | 71.43 | 3.91 | 8.11 |
Structure of an Aspheric Lens
In various industries, ranging from automotive sensors and LED lighting systems to cutting-edge cameras and medical diagnostic devices, the significance of aspheric lenses is steadily growing. These lenses are part of the subset defined by rotationally symmetric optics with a radially varying radius of curvature. Aspheric lenses play an increasingly crucial role in various aspects of the optics, imaging, and photonics industries. This is attributed to the unique advantages they provide compared to traditional spherical optics and spherical elements.
Unlike spherical lenses, which can be specified solely by the radius of curvature that fluctuates radially from the center of the lens, ASP Lenses exhibit a surface with varying local radii of curvature. The definition of rotationally symmetric aspheres often involves a surface sagitta (the measure of the surface shape in relation to a plane), or sag, expressed through an even aspheric polynomial.
Where:
Z: sag of surface parallel to the optical axis
s: radial distance from the optical axis
C: curvature, inverse of radius
k: conic constant
A4, A6, …: 4th, 6th, … order aspheric coefficients
When the aspheric coefficients are equal to zero, the resulting aspheric surface is considered to be a conic. The following table shows how the actual conic surface generated depends on the magnitude and sign of the conic constant, k.
Additional Performance Advantages
To achieve the necessary performance of an imaging lens, optical elements designers frequently resort to stopping down, or increasing the f/# of their design. Although the desired resolution goal is obtained, the approach results in a reduction in light throughput. Using aspheric lenses in the design, however, improves aberration correction and enables the creation of high-throughput systems with low f/#s, while also maintaining excellent image quality. The following table compares two designs: an 81.5mm focal length, f/2 triplet lens (depicted in Figure 2) with all spherical surfaces and the same triplet with an aspheric first surface. Both designs utilize identical effective focal length, f/#, field of view, glass types, and total system length. The table provides a comparison of the modulation transfer function (MTF) at 20% contrast for on-axis and off-axis collimated, polychromatic light rays at 486.1nm, 587.6nm, and 656.3nm. The triplet lens with the aspheric surface demonstrates significantly improved imaging performance at all field angles with high tangential and sagittal resolution values, surpassing those of the triplet with only spherical surfaces by factors as high as four.
Object Angle (°) |
All Spherical Surfaces |
Aspherical First Surfaces |
||
Tangential* |
Sagittal* |
Tangential* |
Sagittal* |
|
0.0 |
13.3 |
13.3 |
61.9 |
61.9 |
7.0 |
14.9 |
14.9 |
31.1 |
40.9 |
10.0 |
17.3 |
14.8 |
36.3 |
41.5 |
“Tangential” and “Sagittal” units are both described as
Benefit of Aspheric Lenses
Unlike conventional spherical optics, aspheric lenses use less elements to enhance aberration correction. An example would be zoom lenses. Zoom lenses typically use ten or more elements while two aspheric lenses can be replaced for a handful of spherical lenses in order to achieve similar or better optical results. The system size and overall cost of production are also potentially reduced.
Aspheric Surface Tolerances
Surface Accuracy:
Radius Error:
Precision Glass Molding:
Precision Polishing:
Diamond Turning:
Molded Polymer Aspheres:
Injection Molding
Selection of Manufacturing Methods for Aspherical Lenses
Fabricating aspherical lenses poses greater challenges due to their complex surface profiles compared to conventional spherical lenses. Various methods are available for producing aspheric lenses, each with its distinct advantages and limitations.
For optical engineers, a crucial aspect is comprehending manufacturing techniques and selecting the most appropriate method based on lens application, performance requirements, development cost, sample cost, production part cost, and project timeline.
Manufacturing of Aspheric Lenses |
Advantages |
Disadvantages |
Volume Recommendation |
Diamond Turning |
Shapes that are complex and freeform |
Not suitable for mass volume |
Prototype, Medium |
Grinding and Polishing |
Diverse range of material selection |
Extended production duration |
Prototype, Medium |
Precision Glass Molding |
Low cost per unit for mass volume |
High Setup and tooling expenses |
Medium, High |
Injection Molding of Plastics |
Low cost per unit for mass volume |
High setup and tooling expenses |
Medium, High |
Aspherical Lenses Material Selection
The choice of materials for aspherical lenses is influenced by factors such as wavelength requirements and manufacturing cost. The following summarizes materials compatible with each manufacturing process.
Manufacturing of Aspheric Lenses |
Capabilities of Materials |
Diamond Turning |
Ge, Si, ZnSe, ZnS, Plastics |
Grinding and Polishing |
Optical glass (CDGM, Hoya, Ohara, Schott), Fused Silica, Low Temperature Optical Glass, Plastics, Ge, Si, ZnSe and ZnS |
Precision Glass Molding |
Low Temperature Optical Glass, Optical glass (CDGM, Hoya, Ohara, Schott) with restrictions, Plastics |
Injection Molding of Plastics |
Low Temperature Optical Glass, Optical glass (CDGM, Hoya, Ohara, Schott) with restrictions, Plastics |
Offerings from Avantier
Application | Type of Lens | Details |
– Explore UV, visible, and IR grade materials | Precision Polished Aspheric Lenses | Excellent for the most demanding applications, our precision polished aspheric lenses are crafted to deliver high numerical apertures, ensuring diffraction-limited spot sizes. |
– Opt for micro-sized aspheres (under 5mm diameters) | Precision Molded Aspheric Lenses | For volume applications such as laser diode collimation, barcode scanners, and optical data storage, our precision molded aspheric lenses offer versatility and reliability. |
– Aspherized achromats combine glass achromat with plastic asphere– Hybrid aspheres seamlessly blend refractive and diffractive properties | Color-Corrected Aspheric Lenses | Discover our unique families of aspheric lenses designed to correct both spherical and chromatic aberrations. Perfect for applications demanding near-diffraction limited focusing performance across multiple wavelengths. |
– Choose from diameters ranging from (5-400mm)– Benefit from hybrid designs for improved broadband performance– Explore a variety of coating options | Infrared(IR) Aspheric Lenses | Addressing the entire infrared spectrum, our infrared aspheric lenses cater to diverse needs, from small molded aspheres for MWIR quantum cascade lasers to families of germanium and zinc selenide aspheres. |
Diameter | 5 – 200mm |
Diameter Tolerance | +0/-0.100mm – +0/-0.010mm |
Asphere Figure Error (P – V) | 3μm – smaller than 0.06μm |
Vertex Radius (Asphere) | ±0.5% – ±0.05% |
Sag | 25mm max |
Typical Slope Error | 1μm – 0.15μm per 1mm window |
Centering (Beam Deviation) | 3 arcmin – 0.5 arcmin |
Center Thickness Tolerance | ±0.100mm – ±0.010mm |
Surface Quality (Scratch Dig | 80-50, 40-20,10-5 |
Aspheric Surface Metrology | Profilometry (2D & 3D) & Interferometry |
Custom aspheric lenses play a crucial role in advancing high-performance imaging across various fields. From aerospace applications like night vision imaging optics to defense imaging systems, and from microscope imaging objectives to semiconductor wafer inspection tools, these lenses serve as indispensable components in precision imaging devices. A notable example is the Smite Cassegrain telescope, which utilizes custom aspheric lenses along with reflective elements to mitigate aberrations and achieve superior resolution.
The advantages custom aspheric lenses bring to high-performance optics are substantial. Particularly, these lenses are an optimal choice when designing systems with a limited footprint, as their inherent characteristics lend themselves well to compact assemblies.
If you are looking for stock options, visit Stock – Aspheric Lenses.
For custom requests, visit Aspheric Lenses page.
Contact us NOW for sales & expert advice.