Project Background
A customer urgently needed two custom silicon lenses, one featuring a highly specialized diffractive surface. Their original supplier had failed to deliver, putting the entire project on a critical timeline. Facing imminent completion without the necessary optical components, the customer sought a new, reliable manufacturer who could provide a quick quotation and ensure successful, expedited production.
Market Application
These specialized silicon lenses are designed for precision photonics and infrared systems. Their advanced nature makes them ideal for high-performance applications in demanding sectors such as defense, medical imaging, industrial metrology, and aerospace instrumentation, where custom optics are essential for system functionality.
Project Difficulties
Mid-Project Supplier Change
The most pressing challenge was the abrupt change of suppliers. The previous vendor’s failure to deliver introduced significant urgency and risk to the project’s timeline, necessitating a partner capable of rapidly taking over and accelerating production.
Technical Complexity
Beyond the time constraints, the lenses themselves presented formidable technical hurdles. One lens, in particular, required a diffractive surface on silicon. This is an exceptionally difficult feature to process, demanding advanced fabrication capabilities and intricate precision to achieve the required optical performance.
How Avantier Helped Silicon Lens Project
Avantier stepped in to address these critical challenges, delivering the high-precision aspheric silicon lenses with demanding specifications.
Aspheric Lens Specifications
- Material: Silicon
- Coating: Infrared anti-reflective (AR) coating optimized for 3.4–5 µm
- Transmission: T > 97%
- Surface Roughness: ≤ 0.01 µm RMS
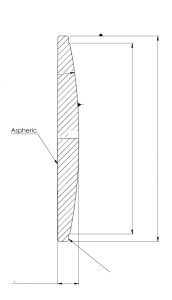
Technical Challenges and Avantier’s Solutions
Avantier successfully overcame several complex technical obstacles:
- Ultra-Smooth Surface Quality and Complex Aspheric Geometry: The aspheric lens demanded an ultra-smooth surface quality combined with intricate aspheric geometry. Avantier utilized single-point diamond turning (SPDT) to precisely machine the aspheric surface precisely, ensuring exceptional accuracy.
- Real-Time Compensation for Deviations: Micro-level deviations caused by thermal effects and mechanical vibrations during processing posed a significant threat to precision. Avantier implemented active, real-time compensation mechanisms to counteract these effects, maintaining the critical optical integrity of the lenses.
- Eliminating Clamping-Induced Stress: To prevent deformation from clamping during machining, which could compromise optical performance, Avantier employed a point-by-point convergence method. This iterative technique gradually eliminated distortions throughout the machining process, ensuring the final lenses met the stringent requirements.
Contact us to schedule a consultation or request a quote—our friendly team is ready to support your project.
Related Content
GREAT ARTICLE!
Share this article to gain insights from your connections!