Key Takeaways of Freeform Optics Fabrication
- Design Complexity: Freeform optics demand advanced modeling tools and exhibit high sensitivity to tolerances.
- Precision Manufacturing: Specialized techniques like diamond turning and magnetorheological finishing (MRF) ensure quality but are time-intensive and expensive
- Metrology Advances: Evaluating non-uniform surfaces requires cutting-edge measurement technologies and custom solutions.
- Cost & Scalability: High prototyping costs and the absence of standardization hinder mass production.
- Integration Challenges: Alignment sensitivity and material constraints necessitate innovative assembly and robust designs for diverse environments.
Freeform optics are custom-designed optical components with irregular surface shapes, enabling precise light manipulation. Unlike traditional symmetric optical components, freeform optics offer unique advantages, such as compactness, weight reduction, enhanced performance, and tailored functionality.
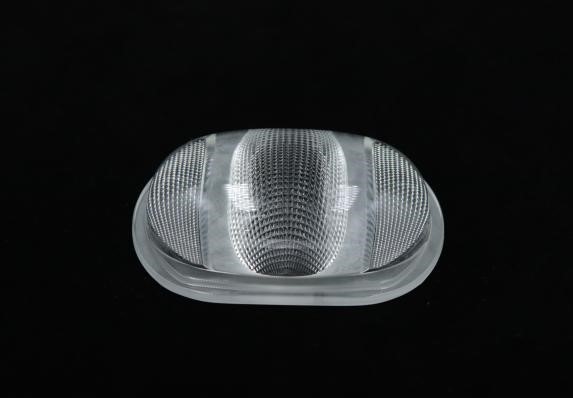
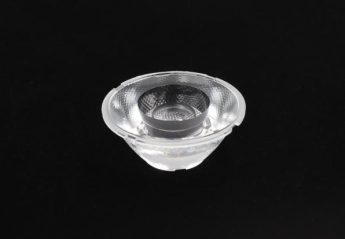
Here’s an in-depth of the challenges associated with freeform optics, categorized into key aspects:
1. Complex Design and Modeling
– Optical Design Software Limitations: Traditional optical design software is primarily tailored to rotationally symmetric systems, lacking advanced features for handling the intricate geometries of freeform surfaces. While software capabilities are improving, challenges persist in ray tracing, wavefront analysis, and optimization.
– Higher Computational Demand: Designing freeform optical components requires substantial computational resources. Techniques like non-sequential ray tracing, genetic algorithms, and machine learning can assist optimization but are resource-intensive and time-consuming.
– Tolerance Sensitivity: Freeform optical designs are more sensitive to manufacturing and alignment tolerances. Even minor deviations can degrade performance significantly, necessitating rigorous design adjustments and stringent tolerance analysis.
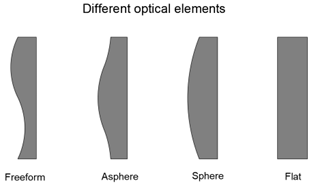
2. Manufacturing Precision
– Diamond Turning Challenges: While diamond turning is widely used for freeform optics, achieving precision on non-rotationally symmetric surfaces is difficult. Errors in tool positioning or surface control can result in imperfections that compromise optical quality.
– Limitations in Traditional Polishing: Standard polishing methods for spherical lenses are unsuitable for freeform surfaces. Advanced techniques like MRF and ion-beam figuring are effective but costly, slow, and require skilled operators.
– Replication Issues: Techniques such as injection molding and imprinting can theoretically mass-produce freeform optics, but maintaining high fidelity to the original design and fabrication and achieving low defect rates remain significant challenges. Additionally, replication often faces material constraints, limiting options for applications with stringent optical or environmental requirements.
3. Metrology and Quality Control
– Measurement Complexity: Evaluating freeform optics requires advanced metrology tools, as traditional interferometers struggle with non-symmetric shapes. Optical Coordinate Measuring Machines (CMMs) and multi-axis profilometers often need customization, increasing costs and lead times.
– Non-Uniform Surface Error Analysis: Measuring deviations on freeform optics is more complex than for spherical optics. Metrics like slope error and form error must be calculated across multiple regions, complicating both initial manufacturing and testing quality inspections.
– High-Precision Alignment: Aligning freeform optics in optical systems is more demanding than with traditional lenses. Slight misalignments can introduce significant aberrations, requiring innovative alignment methods and in-situ adjustments.
4. Cost and Scalability
– Prototyping and Testing Costs: Creating prototypes for freeform optics is expensive due to the need for specialized equipment and skilled operators. Iterative design cycles are slower and more costly compared to spherical or aspherical optics.
– Lack of Standardization: Freeform optics often require custom manufacturing processes, limiting opportunities for standardization and economies of scale. As a result, their use is typically restricted to high-end or niche applications.
– Tool Wear and Replacement: Manufacturing freeform surfaces increases wear on tooling, especially in diamond turning. Frequent tool recalibration and replacement further drive up production costs.
5. Alignment and Integration
– Complex Assembly Procedures: Accurate aligning each part can be challenging in imaging systems with multiple freeform components. This often requires custom fixtures and real-time adjustment mechanisms, increasing complexity and potential points of failure.
– Aberration Sensitivity: Freeform optics are used to correct specific aberrations, but any misalignment can reduce correction quality or introduce new aberrations, severely impacting system performance.
– Thermal and Mechanical Stability: Thermal expansion or mechanical stress can shift alignment. Materials with low thermal expansion coefficients and complex mounts are necessary to maintain alignment under operational stresses.
6. Material Limitations
– Optical Material Constraints: Some traditional optical materials, such as certain glasses and polymers, are challenging to shape into freeform surfaces or lack the thermal stability required for precision applications.
– Environmental Requirements: In extreme environments (e.g., aerospace or underwater), freeform optics must be made from materials capable of withstanding temperature fluctuations, humidity, and radiation. These requirements often narrow material options and necessitate specialized coatings.
– Coating Challenges: Anti-reflective and protective coatings are often applied to freeform optical surfaces. However, achieving uniform coating on non-uniform surfaces like freeform optics can be difficult, potentially affecting optical performance and durability in challenging environments.
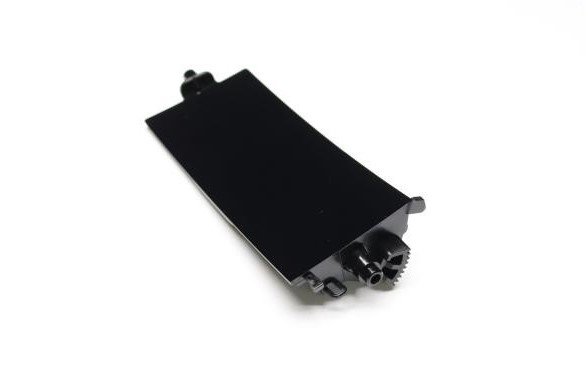
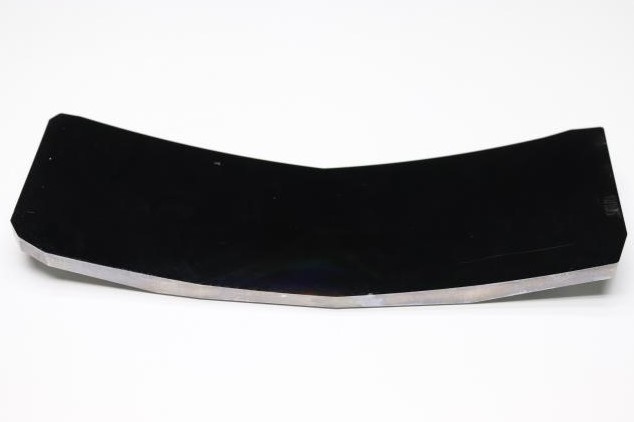
Mastering Freeform Optics Fabrication
These challenges highlight the complexities of designing and manufacturing freeform optics. Each stage—from design and prototyping to production and integration—requires advanced tools, precision techniques, and significant investment.
However, with ongoing advancements in manufacturing processes, computational design, and metrology, the potential of freeform optics continues to grow. Applications in compact imaging systems, augmented reality, and custom sensor solutions are expanding, making freeform optics a promising frontier in optical innovation.
GREAT ARTICLE!
Share this article to gain insights from your connections!