Plastic/Acrylic Molded Aspheric Lenses
Avantier’s molded plastic aspheric lenses are designed to eliminate spherical aberration, making them ideal for applications requiring precision optics at a more affordable price. These plastic aspheres offer a compelling alternative to traditional glass elements, being not only significantly lighter but also cost-effective. With a focus on numerical apertures, our plastic aspheric lenses provide high performance and durability, even in demanding environments. Our advanced manufacturing techniques ensure these aspheric lenses have exceptional quality, making them a practical choice for a wide range of optical systems.
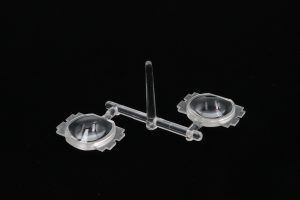
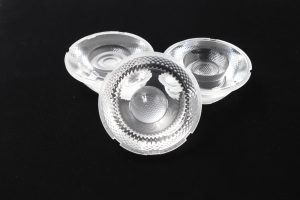
Key Features
- Customization: Tailored designs to meet specific requirements.
- Coatings: Enhance durability and reduce reflections.
- Precision: High-quality molding and polishing processes.
- Performance: Superior light collection with high numerical aperture designs.
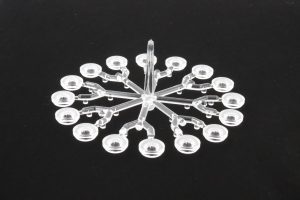
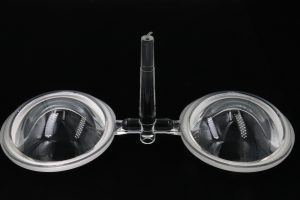
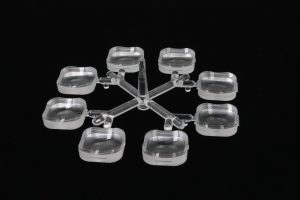
Applications for Acrylic / Plastic Molded Aspheric Lenses
Molded plastic aspheric lenses are widely used across multiple industries, including:
Consumer Electronics: Smartphone camera lenses, VR/AR headsets, and optical sensors.
Automotive Optics: LiDAR systems, head-up displays, and night vision cameras.
Medical Devices: Ophthalmic lenses, endoscopes, and biomedical imaging systems.
Industrial and Scientific Instruments: Laser focusing optics, barcode scanners, and optical sensors.
Augmented Reality (AR) and Virtual Reality (VR): Lightweight optics for immersive headsets requiring distortion-free imaging.
Factory Standard
Basic | Advanced | |
Substrate Material | Plastic / Acrylic | Plastic / Acrylic |
Diameter | ±0.1mm | ±0.03mm |
Thickness | ±0.1mm | ±0.03mm |
Form error (spherical) | Power 5 λ/Irr 1 λ | Power 1 λ/Irr 1/4 λ |
Form error (aspherical) | P-V < 2µm | P-V < 0.5µm |
Decenter | 3′ | 1′ |
Roughness | Ra 0.005µm | Ra 0.003µm |
Customize your Acrylic / Plastic Molded Aspheric Lenses
Avantier is ready to accept customer orders for our molded plastic aspheric lenses, designed to deliver exceptional optical performance at an affordable price. These lenses offer a cost-effective and lightweight alternative to traditional glass optics while maintaining high precision, durability, and superior light collection, even in challenging environments. With customizable designs and advanced coatings, our plastic aspheric lenses are ideal for various applications, from illumination systems to imaging devices. Contact us today to leverage our expertise and advanced manufacturing techniques to provide high-quality optical solutions tailored to your needs.
Manufacturing Molded Aspheric Lenses Using Plastic Material
Manufacturing Molded Aspheric Lenses Using Plastic Material
Aspheric lenses are known for their superior optical performance, which minimizes spherical aberrations, reduces weight, and allows for more compact optical designs. Molded plastic aspheric lenses offer additional benefits compared to glass lenses, including lower production costs, lighter weight, and greater design flexibility. These lenses are commonly utilized in consumer electronics, automotive optics, medical devices, and augmented reality applications. The manufacturing process for plastic aspheric lenses relies on precision injection molding, enabling high-volume production with consistent quality and performance.
Plastic aspheric lenses have become essential in modern optical systems due to their ability to integrate complex designs while maintaining cost efficiency. Advances in polymer material science and precision molding technologies have allowed these lenses to achieve high optical clarity and durability, making them a viable alternative to glass-based aspheric lenses. However, challenges such as material shrinkage, birefringence, and mold wear necessitate specialized process controls to ensure high-quality output.
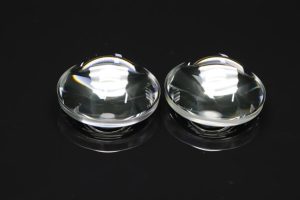
Manufacturing Techniques
Manufacturing Techniques
- Plastic Material Selection
Selecting the appropriate plastic material is crucial for determining the optical performance and durability of molded aspheric lenses. Common plastic materials used include:
– PMMA (Polymethyl Methacrylate): Offers excellent optical clarity (transmittance > 92%) and low-cost manufacturing, commonly used in consumer optics.
– PC (Polycarbonate): Provides high impact resistance and good thermal stability, widely used in automotive and industrial applications.
– COC (Cyclic Olefin Copolymer): Features low birefringence and high UV resistance, suitable for high-precision optical applications.
– COP (Cyclic Olefin Polymer): Exhibits excellent chemical resistance and low moisture absorption, used in medical and bio-optical devices.
– Zeonex and Zeonor: High-performance optical polymers with minimal shrinkage and low dispersion, utilized in high-end imaging systems.
Material selection is influenced by factors such as refractive index (n=1.49-1.59), Abbe number (Vd=30-60), thermal expansion coefficient, and resistance to environmental conditions. Compared to glass, plastics offer easier moldability but usually require additional coatings for scratch resistance and UV protection.
2. Precision Injection Molding Process
The manufacturing of plastic aspheric lenses is conducted through precision injection molding, a process that ensures high repeatability and minimizes post-processing requirements. The key steps in this process include:
– Material Preparation: Plastic pellets are dried to remove moisture (humidity < 0.02%) to prevent defects such as bubbles and surface waviness.
– Injection Stage: Molten plastic is injected into a high-precision mold under controlled pressures (500-2000 bar) and temperatures (180-300°C), depending on the material type.
– Molding Stage: The polymer fills the mold cavity under high pressure, ensuring accurate replication of the aspheric profile with surface accuracy of <0.2 µm.
– Cooling and Solidification: The mold is cooled using precision-controlled temperature regulation (±1°C) to minimize shrinkage and internal stress.
– Demolding and Finishing: Lenses are carefully ejected using non-contact release techniques to avoid surface damage. Post-processing may include edge trimming and surface hard-coating.
Injection molding enables cycle times as short as 10-60 seconds per lens, making it highly efficient for mass production. Advanced techniques such as gas-assisted molding and microcellular injection molding further enhance optical uniformity and reduce internal defects.
3. Mold Design and Coatings
The quality of the mold significantly affects the precision and performance of molded aspheric lenses. Key factors in mold design include:
– Ultra-Precision Diamond Turning: Achieves mold surface roughness below 5 nm RMS for high optical quality.
– High-Strength Nickel or Tungsten Carbide Inserts: Ensure durability and maintain precise shape over high production volumes (>100,000 cycles per mold).
– Anti-Adhesion Coatings (DLC, CrN): Reduce polymer sticking and improve mold longevity.
– Temperature-Controlled Mold Cavities: Ensure uniform cooling and minimize optical distortions.
Proper mold maintenance and periodic re-polishing are essential to ensure lens consistency during extended production runs.
Molded Aspheric Lenses: Product Photos
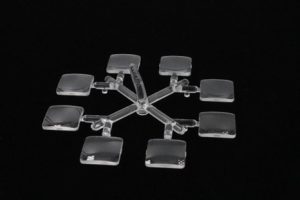
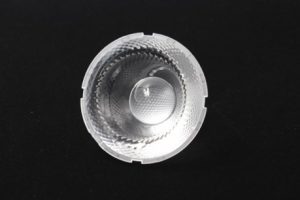
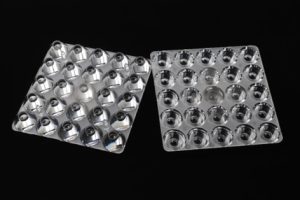
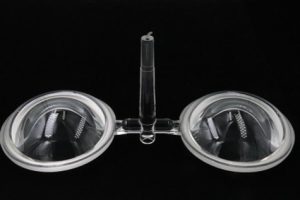
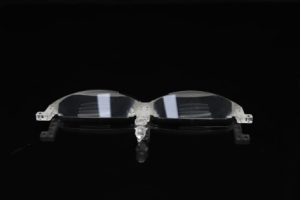
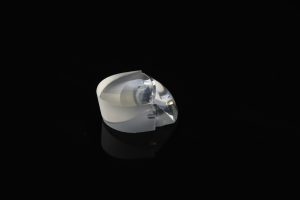
Key Challenges and Solutions
Key Challenges and Solutions for Acrylic Molded Aspheric Lenses
- Optical Accuracy and Birefringence
Challenge: Achieving sub-micron precision while minimizing optical distortions caused by birefringence.
Solution: Optimize mold temperature and injection speed to control polymer orientation, and use cyclo-olefin copolymers (COC) or cyclo-olefin polymers (COP) that have low intrinsic birefringence.
- Shrinkage and Warpage
Challenge: Plastic materials exhibit thermal shrinkage (approximately 0.5-1.5%), which can lead to deviations in the final optical performance.
Solution: Implement multi-gate molding and controlled cooling profiles to achieve uniform shrinkage.
- Surface Hardness and Durability
Challenge: Plastic lenses are susceptible to scratches and environmental degradation.
Solution: Apply hard coatings (based on SiO2) and anti-reflective (AR) coatings to enhance surface resistance and transmission.
- Cost and Scalability
Challenge: High mold fabrication costs for custom aspheric designs.
Solution: Use modular mold inserts and shared tooling strategies to reduce initial investment costs and facilitate efficient production scaling.
Molded plastic aspheric lenses provide a versatile and cost-effective alternative to traditional glass optics, offering significant advantages in high-volume production, weight reduction, and design flexibility. Advances in precision injection molding, material engineering, and surface treatment technologies continue to enhance optical performance. As the demand for lightweight, high-performance optical solutions increases, plastic aspheric lenses will play a crucial role in the evolution of modern optical systems.
Case Study: Plastic Molded Aspheric Lens
Case Study: Plastic Molded Aspheric Lens
Specifications:
- Type: Bi-aspheric surface lens
- Material: Zeinex
- Diameter: 40mm
- Thickness: 20mm
- Surface Accuracy: PV < 1μm
- Processing Method: Mold Forming
Both surfaces of this lens are aspheric and are manufactured through molding. The mold is machined using a single-point diamond lathe, which ensures a high-quality surface shape. During production, parameters such as temperature and pressure are meticulously controlled. This stable production process, coupled with a short processing cycle, guarantees the high surface accuracy of the molded lenses.
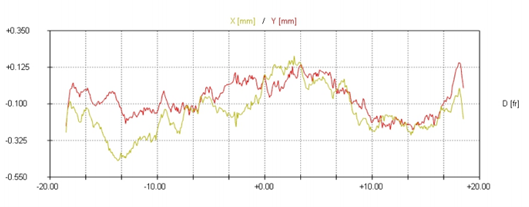
WE CAN HELP YOU!
Contact us NOW for sales & expert advice.