Silicon Carbide (SiC) Mirrors
Silicon carbide (SiC) mirrors are advanced optical components known for their exceptional properties, making them ideal for various applications, including larger telescopes, high-speed scanning systems, and space applications. Here is an overview of SiC mirrors, including their properties, manufacturing methods, and Avantier’ capabilities in producing custom SiC mirrors:
Properties of Silicon Carbide (SiC) Mirrors
Silicon carbide mirrors offer several key advantages:
- Lightweight: SiC is known for its low density, making SiC mirrors significantly lighter than traditional glass mirrors. This property is particularly important for space applications and larger telescopes, where weight reduction is critical.
- High Strength and Stiffness: SiC exhibits high mechanical strength and stiffness, providing excellent structural integrity even in demanding environments.
- High Thermal Conductivity: SiC has high thermal conductivity, enabling it to dissipate heat effectively. This property is essential for maintaining optical performance in high-temperature environments.
- Thermal Stability: SiC mirrors can withstand high temperatures, making them suitable for use in applications where temperature fluctuations occur.
- Thermal Shock Resistance: SiC mirrors are highly resistant to thermal shock, making them durable in conditions with rapid temperature changes.
- Oxidation and Chemical Resistance: SiC is resistant to oxidation and chemical degradation, ensuring long-term stability in harsh environments.
- Low Thermal Expansion: SiC has a low coefficient of thermal expansion, which minimizes the impact of temperature changes on mirror performance.
- Mechanical Strength: While SiC is generally mechanically strong, it can be brittle, so careful handling is required.
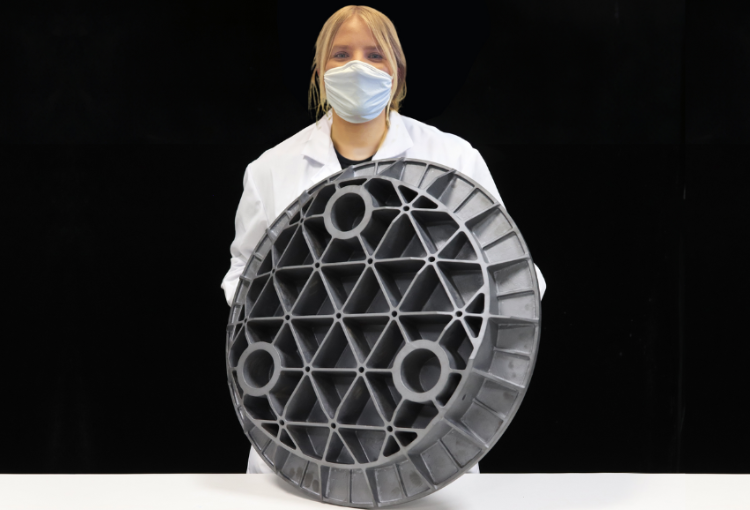
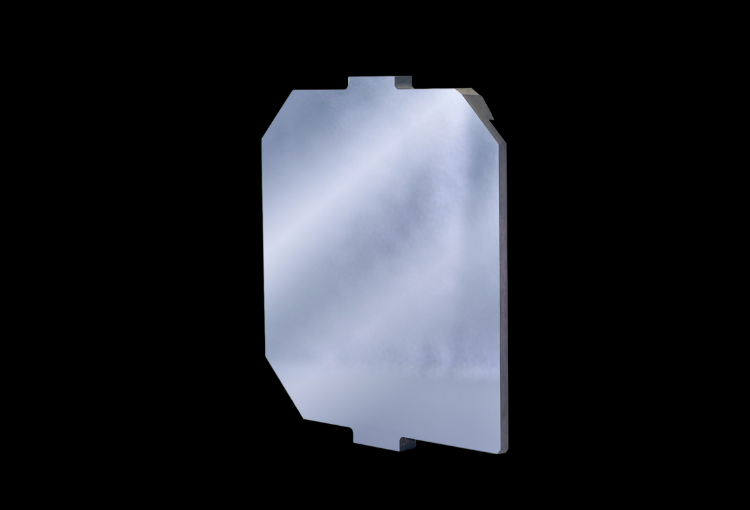
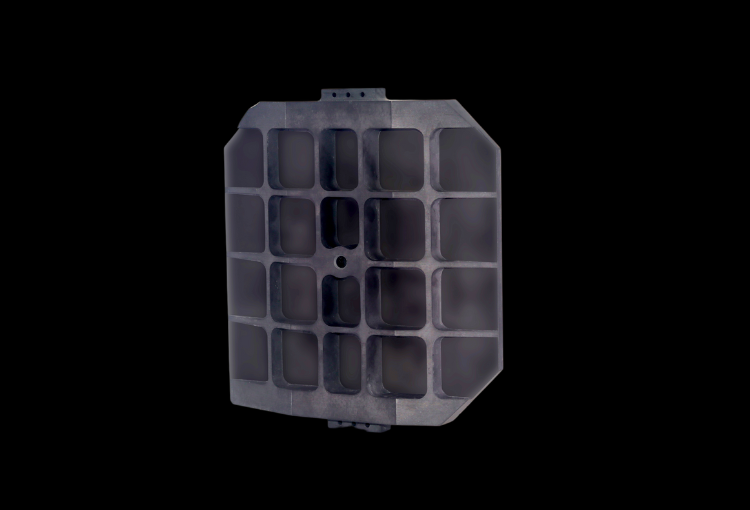
Manufacturing of Silicon Carbide
There are three primary methods for producing Silicon Carbide for optical applications:
- Reaction Bonding: This method involves casting a mixture of alpha Silicon Carbide and carbon, followed by firing. Liquid silicon is then infiltrated into the porous mixture, reacting with carbon to form dense SiC. Reaction bonded Silicon Carbide is cost-effective and suitable for lightweight optical designs.
- Sintering: SiC powder is sintered at high temperatures (above 2000°C) with non-oxide sintering additives in an inert atmosphere and high pressure. Sintered SiC results in a very hard ceramic suitable for optical mirrors but requires extensive machining to eliminate surface roughness.
- Chemical Vapor Deposition (CVD): CVD is used to produce very pure SiC in a face-centered cubic crystal form. This type of SiC has exceptionally high thermal conductivity but is more expensive to produce.
The choice of manufacturing method can impact the physical properties of the SiC, such as density and Young’s modulus.
Manufacturing Challenges and Our Approaches to Address Them
At Avantier, we encounter various challenges in manufacturing Silicon Carbide (SiC) mirrors. However, we employ several strategies to tackle these issues and provide high-quality products to our customers.
Challenges in Manufacturing SiC Mirrors
1.1 Difficult Machinability: SiC is extremely hard (with a Mohs hardness of approximately 9.5), which makes grinding and milling quite challenging. Additionally, diamond cutting can be slow and costly.
1.2 Achieving Ultra-Smooth Optical Surfaces: The grain structure and porosity of SiC can hinder the achievement of ultra-smooth finishes, specifically less than 1 nanometer (nm) root mean square (RMS) roughness. To address this, we require advanced techniques such as chemical mechanical polishing (CMP).
1.3 Thermal Stress and Coating Challenges: The mismatch in thermal expansion between SiC and its coatings can lead to stress and deformation.
1.4 Cost and Scalability Issues: The cost of raw materials and processing SiC is higher than that of conventional materials, such as fused silica. Moreover, the complexity of fabrication limits large-scale production.
Solutions to Manufacturing Challenges
2.1 Advanced Fabrication Techniques
– Reaction Bonding: Silicon infiltrates a carbon preform, creating a dense SiC structure.
– CVD SiC: This method produces high-purity SiC coatings that have better polishability.
– Hot Isostatic Pressing (HIP): This process enhances mechanical strength and improves surface finish.
2.2 Innovative Polishing Techniques
–Ion Beam Figuring (IBF): This technique allows for nanometer-scale material removal, ensuring high accuracy.
– Magnetorheological Finishing (MRF): This non-contact polishing method achieves sub-nanometer smoothness.
– Chemical Mechanical Polishing (CMP): This combines chemical etching with mechanical polishing for optimal results.
2.3 Thermal and Optical Coating Improvements
– Gradient Coatings: These coatings are designed to match the thermal expansion properties of SiC, reducing stress.
– Atomic Layer Deposition (ALD): This ensures that coatings are defect-free and uniform.
–Adhesion Layers: Intermediate layers, such as chromium (Cr) or silicon (Si), improve the bonding of coatings.
2.4 Cost Reduction Strategies**
– Hybrid Materials: By combining SiC with carbon composites, we can achieve lower costs.
– Additive Manufacturing (3D Printing): This method allows for the cost-effective production of complex shapes.
By employing these innovative approaches, we aim to overcome the manufacturing challenges associated with SiC mirrors and deliver exceptional products to our clients.
Specifications – Custom Silicon Carbide Mirrors
Size | 25 mm – 800 mm |
Surface Shape | Flat (typical), Sphere, Aspheric |
Surface Flatness | up to λ/100 RMS |
Coatings | Al, Ag, Au & High Laser Damage Threshold Dielectric Coatings as needed |
Lightweight SiC Mirror Applications | Telescopes, Laser Scanning Systems, Semiconductor and Lithography Systems, Defense and Military Applications, etc. |
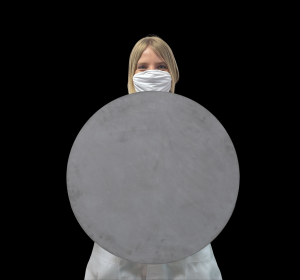
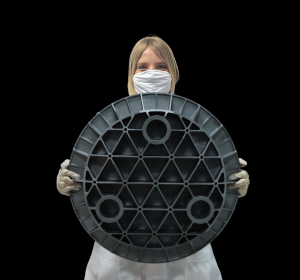
Custom Design Example 1
- Diameter: 500 mm
- Thickness: 100 mm
- Coating: 95% reflectivity @ 400–12,000 nm
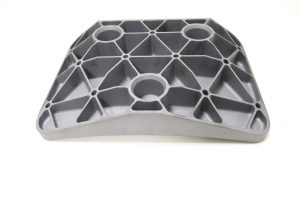
Custom Design Example 2
- Dimensions: Length 379 mm, Width 260 mm, Thickness 85 mm
- Dimension Tolerance: ±0.1 mm
- Clear Aperture (CA): 90%
- Surface Quality: 80-50
- Surface Accuracy: RMSI < 16 nm
- Coating: Protective gold
- Reflectance (Rabs): >95% @ 400-12,000 nm
- Angle of Incidence (AOI): 0-4.5°
Custom Silicon Carbide Mirrors at Avantier
Silicon carbide (SiC) mirrors are critical to high-performance optical systems, especially in extreme environments like space exploration, semiconductor lithography, and advanced defense applications. At Avantier, we specialize in producing custom SiC mirrors tailored to the exact specifications of each client—whether for large telescopes, high-speed scanning systems, or next-generation aerospace and photonics platforms.
Despite the challenges in fabricating SiC mirrors, advancements in polishing methods, hybrid designs, and coating techniques have pushed their capabilities further than ever before. Avantier utilizes precision machining and state-of-the-art metrology to deliver SiC mirrors with a wide range of sizes, shapes, and optical coatings. As additive manufacturing and surface engineering technologies evolve, our mirrors are poised to meet the demands of increasingly sophisticated optical systems.
If you’re seeking custom SiC mirrors or design support, our team is ready to assist. Avantier’s expertise ensures high-quality results for your most demanding optical requirements.
WE CAN HELP YOU!
Contact us NOW for sales & expert advice.